2017,全球经济处在大变革时期, 转型升级是企业不可逃避的问题。
1933年,丰田创始人丰田喜一郎开始研制汽车,2014年,丰田汽车世界品牌排名第一,品牌价值是349.03亿美元。
近年来,日本丰田的成功之道被不断总结,并且成为无数企业学习和效仿的标杆:西门子、三星、LG、大众等世界一流企业践行并创新精益;华为、美的、福田汽车、中国南车等国内先进企业学习和效仿,希望运用精益打造低碳运营模式,实现企业再造升级······
精益生产,正在成为企业发展转型的利器。
音频录制 | 孙啸晶
来 源|正和岛(ID:zhenghedao)
为什么是丰田?
1933年,当丰田喜一郎开始研制汽车时,通用汽车公司和福特汽车公司早已是车界望尘莫及的大佬.2007年后,丰田年产汽车近950万辆,取代通用汽车公司76年的霸主地位,成为全球最大汽车制造商。
2012年,在经历了短暂的低潮后,丰田重返全球汽车制造第一的宝座,汽车累计产量突破2亿辆大关。
2014年,丰田公司的营业收入是2564亿美元,虽然少于大众汽车的2615亿美元。但丰田公司的利润却是大众公司利润的1.5倍。这一年丰田汽车在世界品牌排名第一,品牌价值是349.03亿美元。
丰田“速度”正在悄然改写世界汽车市场的格局。
丰田持续辉煌,缔造传奇的背后原因在于“丰田生产方式(TPS)”!
为什么要学习丰田生产方式——精益生产?
1985年,为了揭开日本丰田汽车工业成功之谜,美国麻省理工学院开启了“国际汽车项目计划”研究。用了5年的时间对14个国家的近90个汽车装配厂进行实地考察,对西方的大批量生产方式(Batch Production)与日本的丰田生产方式(Toyota Production System, TPS)进行对比分析,最终出版了《改变世界的机器》一书,书中把丰田生产方式正式命名为“精益生产”,同时被誉为“改变世界的机器”。这是继泰勒生产方式(科学管理法)、福特生产方式(大批量流水线)之后人类现代生产方式的第3个里程碑。
精益生产的提出,把丰田生产方式从生产制造领域扩展到产品开发、协作配套、营销网络以及经营管理等各个领域,贯穿于企业生产经营活动的全过程,使其内涵更全面、更丰富,对指导生产方式的变革更具针对性和可操作性。
这个研究成果在汽车行业内引起轰动,掀起了一股学习精益生产的狂潮。自此,日本丰田的成功之道便被不断总结,并且成为无数企业学习和效仿的标杆:西门子、三星、LG、大众等世界一流企业践行并创新精益;华为、美的、福田汽车、中国南车等国内先进企业学习和效仿,希望运用精益打造低碳运营模式,转变企业发展方式,实现企业再造升级!
精益生产,正成为企业发展转型的利器。
什么是精益生产?
精益生产方式的基本思想可以用一句话来概括,即:Just In Time(JIT),翻译为中文是"只在需要的时候,按需要的量,生产所需的产品"。
很多人试图从各个方面去解读精益生产方法。相对比较详尽的是杰弗瑞·莱克的著作《丰田模式》,书中总结了精益生产方式的14项管理原则:
原则1:管理决策以长期理念为基础,即使因此牺牲短期财务目标也在所不惜。
原则2:建立连续的作业流程以使问题浮现。
原则3:使用拉动式生产方式以避免生产过剩。
原则4:使工作负荷平均(生产均衡化),工作应该像龟兔赛跑中的乌龟一样。
原则5:建立立即暂停以解决问题、从一开始就重视质量控制的文化。
原则6:工作的标准化是持续改善与授权员工的基础。
原则7:通过可视化管理使问题无所隐藏。
原则8:使用可靠且已经充分测试的技术以协助员工及生产流程。
原则9:培养深谙公司理念的领袖,使他们能教导其他员工。
原则10:培养与发展信奉公司理念的杰出人才与团队。
原则11:重视合作伙伴与供货商,激励并助其改善。
原则12:亲临现场,彻底了解情况(现地现物)。
原则13:制定决策时要稳健,穷尽所有的选择,并征得一致意见;实施决策时要迅速。
原则14:通过不断省思(日语是hansei,意指“反省”)与持续改善以成为一个学习型组织。
当然,精益生产远不是一项工具,它是一种理念,一种文化,一种自治的系统。
现在全球处在大变革时期,丰田汽车身处其中,自身也是如履薄冰。只是它拥有拥抱变化、即刻调整、不断优化的精益文化。这使它能在任何逆境中突围。而且,工业的标准化为持续改善奠定了非常扎实的基础。
相比之下,国内的企业总是想着弯道超车,但是很多时候大家忘记了,弯道超车是需要基础的,不管互联网时代还是工业时代,沉下心来做事,追求产品品质,才是王道。
从这个角度看,无论是制造业企业,还是互联网企业,都需要沉下心去,好好修炼丰田的精益生产。
2017年4月16日,8天7夜,邀您一同前往的“精益起源”的日本,在丰田唯一对外开放的研修道场,实战演练,体悟原汁原味的TPS,聆听在丰田服务超30年的实战专家的精彩剖析,一对一为您解开企业发展中的困惑!
课程价值
“原汁原味”的丰田TPS实战知识体系 ,真正全景再现丰田人财育成体系
在丰田旗下唯一对外开放研修道场,以身悟道
独一无二、真正的“零距离”生产现场教学
道场实战演练,一对一的现场“把脉”
在丰田服务超30年的资深实战专家们
同团企业家互相交流,分享精益管理智慧与经验;8天7夜,培养深厚感情,拓展高端人脉
精益文化体验,切身体味精益之魂
研修完结,指导未止,企业回访交流,定制精益管理方案
核心师资
金大一
日本丰田MIC生产性研究所 董事
天津大学管理学院 客座教授
常年致力于丰田式精益生产管理模式的研究与咨询,累计为中国企业节约成本超过100亿人民币。
专注于日本的制造业经营模式的梳理及研究,多年来带领专业团队在日本、中国、泰国、越南等地实施多个大型咨询项目,在制造业的规划与设计以及体系搭建等方面具有非常丰富的实战经验。
钻研 、开发丰田精益生产管理理念,结合中国文化特点,注重在中国制造业的推广与落地。
吉永雅文
丰田生产调查室 海外支援专家
吉永先生于1967年丰田自动车入职,在日本丰田工作长达40余年。是丰田TPS训练专家、TPS推进专家组成员,天津协丰会专家。1985年起长期担任丰田海外工厂TPS推广与指导,先后负责过土耳其南非、中国等新建工厂,进行TPS体系搭建。2007年调任至丰田日本本部生产调查室,对丰田集团旗下所有整车工厂及供应商进行TPS指导。
吉永先生是丰田在海外自主研活动及TPS道场建设主要的平台搭建者,对于丰田TPS在海外的传播、建设做出卓越的贡献。一生坚持实践TPS,是TPS在全球工厂发展的见证者、建设者、是现存获得大野耐一师承为数不多的日本TPS专家之一。
小藤行治
丰田MIC-J(服务丰田34年) 副社长
丰田集团TPS自主研修会 干 事
小藤老师在日本丰田集团岐阜车体工作长达30余年。担任过冲压、焊接、涂装、组装、TPS推进式部长,有着多年的丰富现场经验。后被调任至丰田MIC-J,负责丰田岐阜车体内部员工培养及海外人财培养。
小藤老师建树于现场问题的发现,提高设备的可动率,人与自动化生产线的效率结合,作业动作的优化,以及提高生产品质的生产线改善。
小藤老师有多年赴海外企业咨询,优化的经验,曾赴中国,韩国,泰国等国家。
部分参访标杆企业概览
旭自动车工业工厂
※ 为了节省人力成本,多年致力于“多能工”的培养
※ 确定每一道工序的原单位,“一个流”进行加工,将工序间库存降至最低※ 现场生产进度全过程可视化
※ 为了保证品质,减少员工负荷,常年致力于“POKAYOKE”&简易自働化※ 作为丰田岐阜车体的供应商,如何进行KANBAN拉动将成品及材料库存降低。
鹫崎工厂
※ 一个毛利只有1%的企业是如何生存下来的?见证企业28年的持续成长。※ 零距离观察分秒改善※ 为了保证最高品质60年如一日的防错装置改善历程※ 为了不断节省成本,如何真正的快速(SMED)换线※ 先进模具制作方式※ 中国导入了N年都未曾成功的神秘看板,是如何在加工商与供应商之间简单的传递※ 更能深刻理解看板的原理及作用以及运作方式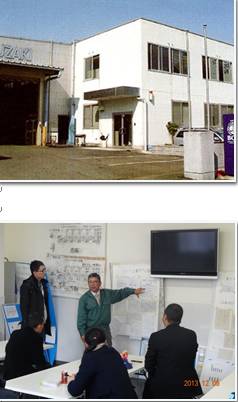
龟山制铁厂
※ 彻底的现状调查&分
※ 由点→线→面的多年来的改善过程
※ 不放任何多余的零部件现场
※ 当放生问题时,第一时间就能够做出反应的组织体系
※ 对于品质以及生产效率的苛刻管理
※ 从开始改善到维持改善,从亏损到完全盈利的艰辛历程
MIFUNE 工厂
※ 作为丰田二级供应商,工厂遵循TPS生产管理模式运作※ 会长带领参观,工厂内部允许拍照及摄像(丰田系工厂唯一一家)※ 冲压机床实现快速换模,利用平准化看板箱,进行单件流生产,采用简易 自働化以及防错装置对品质进行管控※ 保全及仓库管理做出自身特色
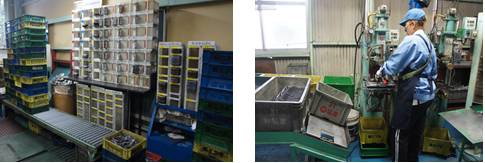
丰田产业技术纪念馆
※ 丰田产业技术纪念馆诠释了整个丰田发展的历史,隐性的告诉世人丰田的成功不是偶然,而是必然。※ 这里沿用了丰田发源地丰田织机的旧厂址,从织机到汽车这个巨大的转变的每一步坚实的脚印,都在这里留下了深深的痕迹※ 这里告诉了世人,改善是可以造就一个又一个的神话,非常适用于现在的中国企业家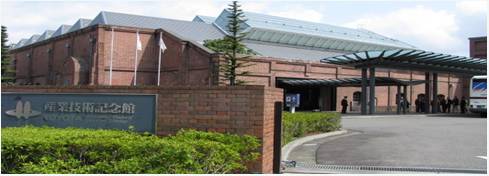
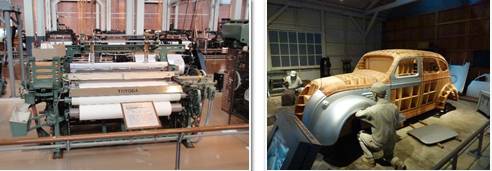
往期课程学员感悟
丰田是世界级企业,TPS的管理思想对我们启发,尤其是人“财”培养的理念。中国与日本的文化有很多相似之处,管理上有很多可以借鉴的地方。这次丰田之旅,收获非常大,感谢你们!
—— 中美史克全球副总裁
感叹日本员工分秒必争的紧凑式工作模式以及细微之处的改善所凝结的无限智慧。与其抱怨员工素质,不如提高管理水平,引导及培养员工的改善意识。企业生产要具备匠人精神,细微之处也要坚持改善,精益求精。出现问题,一定要追根到底,及时解决。解决问题固然重要,但更要注重方式方法,不计成本的改善是一种资源的严重浪费。
——京东方科技集团首席顾问
我们接触TPS比较晚,是在2010年才有了接触,我连续去了日本丰田2次,令我震惊的是短短的时间,他们现场的变化都能让我看出来。加上我们这个行业的激烈竞争,我真的感觉,我们如果不尽快走上TPS之路就一定会死,会被淘汰。
我们和远发合作了好几年了,现场的变化是让我吃惊的,我很庆幸我们走了这一步,并且现场的变化让我们坚信我们走对了路,并且我们会一步一步坚实地走下去。
——雅迪天津基地负责人
和岐阜车体相比,我们的管理者投入现场和时间太少。丰田强调的三现主义让我感触颇深。我也去过很多欧美的现代化工厂参观,看得更多的是现代化设备,而岐阜工厂却不同,岐阜工厂永远不是买最先进的设备,而买最适合自己的设备。我想比起盲目的投资设备,了解我们真正需要什么才是更重要的。岐阜车体背后的管理才是我们中国企业所真正需要的。
—— 北京阀阀木门总裁
行程预览
4月16日
启航,开启中国制造业“精益”寻道之路!
研修:丰田生产方式的导入
4月17日
4月18日
研修:丰田“三现主”及“5W"分析法
研修:JIT+自动化
4月19日
研修:改善及标准作业+实战演练
4月20日
4月21日
体验世界级工厂的精益水平
4月22日
名古屋——文化体验之旅
返回中国,精彩旅程结束
4月23日
PS:讲真,全产业链都应该去学丰田。效率不仅是后端制造的事情,前端更需要深刻理解供应链、理解订单如何转化为交付产品。
再PS:中国老板都很强,中层和基层员工相对比较弱,要让后者与老板在同一个频道上对话,最好的办法是,带管理层一起来感受、改变!!这种决心和投入才能给公司带来巨大影响!
每班限额15-24名,so,欲购从速!
报名须知
招生对象
制造企业董事长/总裁/总经理、副总裁/副总经理
生产部长、生产经理、运营经理、设备经理、质量经理
物流经理、供应链经理、IE工程师
持续改善经理、精益推进办公室主任、变革管理部经理;
物流经理、供应链经理、IE工程师
收费标准
原价 41800 元/人
*正和岛海客报名立减1000元/人
*正和岛岛亲报名立减2000元/人
报名需预付订金5000元/人
费用包含
日方邀请函、日本食宿费(享受单间客房),道场研修费、认证费,保险费(保 险额度最大3000万日元)等;
费用不含
往返国际机票,在日期间个人消费以及赴日签证费用;因自然灾害、战争、罢工等不可抗力因素所产生的费用。
咨询热线
行程、补款、订单、发票相关问题
手机\微信 张小姐 : 13699177723
预定流程
支付定金
↓
24工作小时之内
工作人员会与您联系介绍具体的
行程细节
以及机票与签证的代办事宜
↓
确认出行,定金支付后一周内交齐尾款
*截止报名日:2017年3月18日
*退款事项
定金支付7天内无理由退款,7天后不予退款;如因签证拒签申请退款:
3月18日之前,退全款100%;3月18日-3月31日,退全款50%;4月1日-4月7日,退全款20%;4月7日零时起不接受退款。
点击“阅读原文”
与优秀企业家来一场追根溯源的朝圣之旅吧!
▪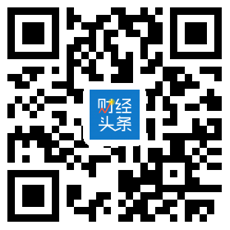
4000520066 欢迎批评指正
All Rights Reserved 新浪公司 版权所有