《中国核工业报》 葛维维|文
“N”代表 New,代表Number,也代表 NPIC(中国核动力研究设计院英文缩写),36 是材料的编号。核动力院的科研人员将探寻新材料的美好愿景与几十年脚踏实地的科研探索相结合,于是便有了N36——中国自主燃料元件高性能锆合金包壳材料的诞生。
10月23日,核动力院与西部新锆材料科技有限公司签订了技术转让合同;11 月 23 日,N36 锆合金管棒材通过转批量化阶段工艺评审。这不仅意味着中国第一个自主研发的商用核电站燃料元件的锆合金研发成功,也意味着中国自主研发的锆合金材料具备了工程化应用条件,更为我国核电事业发展以及“华龙一号”走出去奠定了坚实基础。
燃料包壳被认为是燃料元件的“外衣”,那么,科学家是如何打造中国自主燃料元件的完美“外衣”的?近日,记者来到了核动力院,探寻答案。
夹缝中闯出一条新路
众所周知,燃料元件包壳被称为反应堆的第二道安全屏障,其作用就是将放射性物质包裹在里面。由于特殊而苛刻的运行环境,包壳材料必须具备耐辐照、耐高温、耐腐蚀性等综合要求。
从最开始的不锈钢材料到三代锆合金,国外在包壳材料方面已经走过了 60 多年的研发、使用历程,而中国始终没有形成自己完整的自主材料研发体系。“国内的燃料包壳市场长期以来被法国M5、俄罗斯E635、美国ZIRLO等为代表的高性能锆合金包壳材料占领。”核动力院科技处副处长许余告诉记者。
可以想象,没有自己的包壳材料,燃料元件的自主化无疑是被“卡住脖子”。长期以来,中国只能实现燃料元件的本地化生产,而不能实现燃料元件的自主化研制。作为中核集团唯一专业从事燃料及材料研究的核动力院,将“不被别人牵制,研制出完全自主知识产权的高性能锆合金包壳材料”作为自己的目标。
任何科研成果的取得都不是一朝一夕之功,在材料的研发方面尤甚。“法国、美国已经在材料研发方面申请了很多技术专利,我们要研发自己的锆合金材料,就得在国外专利的夹缝中找出一条新路。”中核集团CF项目副总设计师、N36锆合金研发团队负责人赵文金回忆。
道阻且长,行则将至。尽管国内技术基础薄弱,核动力院负责材料研发的四所科研人员却没有气馁,而是以核燃料及材料国防科技重点实验室为平台,从最基本的成分设计、优选开始,一步一步向前摸索。没有现成的工艺实验设备,技术人员就集思广益自己造;没有可借鉴的工艺方法,技术人员就反复开展各类工艺实验。这项工作始于国家“八五”时期,由周邦新院士首先提出,历经三十几年的不懈探索,科研人员先后完成了显微组织、静态腐蚀、拉伸、疲劳、蠕变、焊接等一系列的实验攻关,成功研制出一种性能优异的合金材料——N36。2010年5月,在首次在中国召开的锆合金国际会议上,中国的锆合金研究创新成果,也引起了国内外同行的高度关注。
“拼”出一套研制设备
就在中国的锆合金研发取得突破性进展的同时,2010 年,为保障国家能源供应的长期安全,确保国家核电技术“走出去”顺利实施,中核集团启动了CF系列自主品牌核电燃料元件的研发项目,由核动力院牵头,其中N36特征化组件入堆辐照为重要里程碑节点。这个项目的立项为N36锆合金的研发注入一剂“强心针”,极大地促进了研制工作进展。
然而,尽管实验室锆合金研究技术日趋成熟,要真正实现从实验室研究到工业化规模运用的转化,绝不仅仅是简单的工艺规模放大。赵文金告诉记者:“当时国内连适用于新型锆合金研制及小批量生产的设备都没有,更别提规模化的生产工艺了。”
没有研制加工设备就“拼”出一套研制加工设备。眼前的困难没有吓退这群一直秉承“自主创新、勇攀高峰”理念的人。他们迅速联系了国内其他合金生产企业,同时确立了工艺研究、性能研究、腐蚀性能和合金开发四个专业攻关小组。
除了工艺上的考验,时间的控制也有要求。核电站的换料时间固定,错过一轮换料必须再等12个月,整个项目的进度必然受到严重影响。因而必须在电站换料之前成功研制出N36特征化组件并通过专家组的验收。
一边是大力协作“拼”出来的研制加工设备,一边是要同时间赛跑,这场攻坚战注定艰难。为了匹配合适的生产设备,赵文金多次与厂家协调沟通,引进先进设备,让生产工艺最大程度地优化;为了赶进度节点,现场技术人员和工人一起实行倒班制度,太累了就趴在桌子上眯一会儿又或在地板上躺一会儿。冬天,在零下4 度的厂房里,他们和工人们一起扛起冰冷的管坯;夏天,40 多度的闷热厂区依然可以看到他们的身影……正是这种认真负责、不畏艰苦、长期坚持的作风,2011 年12月,赵文金带领团队成功研制出 N36 特征化组件用N36棒材并通过专家组验收。
2012 年 6 月,首批 N36 特征化燃料组件进入秦山核电进行入堆辐照考验。没有条件,创造条件也要上,首批 N36 材料在拼出来的一套设备上,完成了华丽的转身,赢得了这场攻坚战的胜利。
核材料没有第二名
今年 11 月 23 日,在 N36 锆合金管棒材通过转批量化阶段工艺评审汇报会上,作为汇报人的赵文金几度哽咽。在担任项目技术负责人的这几年里,赵文金的头发几乎全白了。赵文金说,泪水不是因为经常和大家一起在现场干活到凌晨一两点的辛劳而流,也不是因为炎热的夏天在40多度的车间里躬身查看机器、仔细研究工艺的劳心,而是因为核动力院人坚守三十多年面对困难始终不曾放弃。
核动力院设计所五室主任陈平说:“核材料没有第二名。市场是以指标说话的,不管你前期投入了多少,你的材料不是最好的,别人就不会选择你。”赵文金团队深谙这一点,因而在任何时候,他们都没有放弃过对研发高性能质量材料的追求。
2011年,工厂生产出来的第一批锆合金管子经过检测有裂纹。生产认为,这种等级的裂纹不会影响下一步的制造。赵文金在仔细检查后决定:必须停下来,重新生产!重新生产,原材料报废,经济损失巨大,更有可能赶不上计划进度。在专家讨论会上,大家的意见分歧很大,赵文金坚定地说“:既然让我负责技术,请大家尊重我的意见和决定!”最终,赵文金凭着在几十年材料领域的研究经验和坚定信念,赢得了所有人的支持。
在下一步的制造过程中,赵文金团队严格按照质保管理体系的要求,加强了对每个过程的控制。在有着20多道非定级工序的生产中,他们将最后成品的裂纹控制在了微米级别。事实证明,赵文金的坚持是有意义的。从最后的检测结果来看,第一批材料即便经得起检测,但经过加工之后,成品率也几乎为零。如果不是及时报废第一批材料,进行了第二批材料的重新生产,根本满足不了 CF项目的进度要求。
从2010年到2017年,N36锆合金研发经历了工艺探索、工艺放大、工艺改进到工艺定型等阶段,投入材料从 260 公斤级提升到 5000 公斤级。每一步的放大过程中,在质量方面遇到的挑战都不计其数。而团队始终坚持核无小事,没有第二,只有第一。也正是核动力院这份追求卓越的勇气与信念,换来了今天的成功。
今年 9 月,N36 特征化组件在国内首次完成了为期四个循环的商用核电站随堆运行考验。与此同时,采用N36 包壳材料的先导组件也已经完成两个循环的随堆考验。检查结果显示,N36锆合金作为包壳材料的燃料棒在结构稳定性、辐照生长关键指标上均优于其他包壳材料。历经三十几载磨砺,N36,这个中国首个自主研发的高性能锆合金品牌,即将出鞘,并将走向世界。
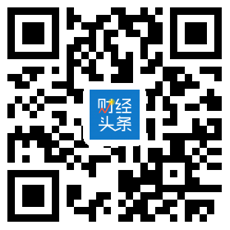
4000520066 欢迎批评指正
All Rights Reserved 新浪公司 版权所有