对于汽车来说,安全就是最大的豪华,而在电驱动系统的安全领域,电控技术扮演着核心角色。2024年10月25日,在第十二届汽车与环境创新论坛上,智新科技股份有限公司研发中心电控开发专业总师王闻宇谈到,智新科技已顺利取得单电机控制器功能安全ASIL C级别的权威认证,并计划深入探索小三电融合架构下的功能安全新挑战。
与此同时,确保安全停车并非终点,智新科技更致力于实现系统的容错运行及全面的健康诊断与预警。对于位置传感器的容错需求,创新研发了无位置传感器矢量控制算法,能在常规工况下无缝切换,有效防止动力损失。针对主要功率器件的寿命挑战,研究基于结温预测和电容监测的预警系统,以期提前干预,延长器件使用寿命。
此外,为解决轴电压引发的轴承电腐蚀问题,已采用陶瓷球轴承作为解决方案,同时也在不断探索通过优化调制策略,来降低轴电压,进一步延长轴承寿命,甚至寻求完全替代陶瓷轴承的可能性。
以下为演讲内容整理:
智新科技技术成果
10月,岚图知音上市,并在随后的24小时内获得了超8000台订单。其中,岚图首次推出的800V产品,也就是超长续航版,占据了总订单量超过50%的份额。20万级别的价格是岚图迄今为止最为亲民的产品,但其表现丝毫不弱于之前的产品,尤其是三电系统。岚图为知音的三电系统提炼了一个关键词叫985学霸,其中9指的是901公里的超长续航,8指的是800V高压碳化硅平台,5指的是5C快充。
电驱动总成方面,岚图知音凭借高达92.9%的高能效区间比,获得了中汽研“能效之星”的认证,并且在该领域内位居中国量产车型之首。此外,岚图知音还提供了宽敞的车内空间,其空间利用率超过86.7%。岚图知音还获得了C-ECAP白金牌的金银座舱认证,NVH的表现也同级领先。
为岚图知音整车产品力提供有力支撑的是智新科技研发的iD4系列新能源电驱动系统。该系统作为东风公司首款深度集成架构下的电驱动总成,展现了出色的兼容性与技术实力。它不仅兼容800V和400V两种电压平台,还兼容同步电机与异步电机,实现了高效率、高功率密度以及超静音等多重优势。在800V同步平台下,该系统的CLTC工况效率高达91.5%,功率密度超过3.25kW/kg,主阶次噪音在1米声压级下低于68分贝。
早在2023年初,在车型刚规划时,我们就和岚图深度协同,进行了产品的定义。我们分析了终端客户的期望,包括续航里程、购车成本、驾乘体验、动力性和智能化。岚图提出的整车需求包括效率高、充电快、舒适静音、安全可靠、动力强劲、具备智能化和自诊断的特性,同时成本要低。
据此,我们得出结论,动力总成必须做到高压、高速、高效、舒适、安全、智能,同时必须是一款经济的产品。一款要求如此高的产品开发周期只有12个月左右,并且这是一个系列化产品,里面共有4款。在我们的项目刚启动时,800V产品收到了一个通知,说量产的时间要提前2-3个月。由于我们的电驱动总成是深度集成的架构,这决定了我们一旦出现问题,其质量成本会进一步提升。为了平衡开发速度和质量,我们决定优化开发流程和体系,把验证过程向左移,大幅度提高仿真在开发中的占比,同时大幅提高了早期评审的密度。
电磁方案是电机设计的灵魂,为了获取最优的电机方案,我们建立了基于CLTC循环工况的综合效率仿真平台,在该平台中不仅能综合考虑效率外特性,NVH等因素,还可以把电机和电控进行联合效率仿真。
我们采用了一种基于响应面的多目标优化算法,这个算法里可以得到最优解的前沿,这个前沿代表一系列方案,从这些方案中优中选优,最终我们从大约5000-6000个方案中选出了最优的设计参数组合。通过这些方法,我们有效降低了电机的铜损和铁损,单电机的实测效率最高超过了98.1%,CLTC的工况效率超过了96.5%。
电控方面,我们采用了自主设计与量产的高压碳化硅功率模块,该模块采用了深沟槽技术的碳化硅芯片,同时采用双面银烧结技术,该技术比传统的技术降低了20%的热阻,同时将芯片的连接强度提升300%。我们在四芯片并联的情况下能够输出360A的有效值,六并联的情况下输出480A的有效值,可以匹配最多260kW级别的功率输出。
故障保护是碳化硅驱动的难点,因为碳化硅的开关速度快、芯片面积小,一旦发生短路,保护不及时很容易就损坏了。为了配合这款功率模块,我们开发了专用的碳化硅驱动保护技术,通过混合关断技术实现了安全可靠的故障保护。同时,我们采取了优化效率的调制技术,首先通过DPWM技术,降低了30%的开关次数,再结合智能载频优化,最终实现了40%开关损耗的降低。我们还配合电机的电磁方案进行了深度的过调制优化,目前电压利用率可以达到105%,在高速循环工况下,可以降低电机相电流7%。
在系列优化的过程中,我们有一个深刻的体会,即没有最优的控制方法,只有最优的标定。在寻优过程中,最后一公里的工作经常都是通过标定来实现的。比如在探索过程中,我们发现过调制的系数提高以后,NVH效率甚至是稳定性都会出现问题,于是通过深度标定的方法解决,既能寻找到效率最大的扭矩曲线,也能找到调制深度、效率和稳定性之间的关系。通过这些协同优化,实现了单电控最高效率99.4%以上,比起IGBT器件降低了约60%的损耗。
针对机械传递损耗的追求,我们采取了一系列手段。首先采用最优的轴承预紧力,平衡了轴系合力,减少系统的变形发热,降低轴承的效率损失,同时通过合理的齿轮参数设计减少摩擦付。我们还开发了一种低黏度的新油品,通过精确的润滑技术降低搅油损失。此外还采用了齿面超精摩和低摩擦轴承等技术,最终在成本和效率之间找到了平衡点。
高功率密度层面,功率密度等于功率除以体积或功率除以重量。要提高功率密度,首先要在总成结构上做文章。传统的电驱动总成、电机、电控和减速器都有独立的外壳,它们之间的水道和油道需要独立连接。但在新一代电驱动总成中,我们通过深度的集成和设计形成了一体化全内置的循环结构,同时集成壳体轴承做刚度提升、热套变形控制,提高了总成模态和支撑刚度。
在液压油路和水路集成后,我们发现不再需要额外的油管和连接件,不仅简化了总成的外形,还可以进一步降低设计成本。通过这些手段,我们不仅实现了总成重量减轻7公斤,功率密度提升9%,还在总成的包络尺寸上有了很大优化。
总成架构上,除了一体化铸造壳体外,在电控部分也采用了多功能模块集成的复杂的结构设计。我们采取了灌封一体化电容和滤波器,直接把电容和滤波器都灌在支架上,配合驱动控制一体板,形成了高功率密度的逆变砖。在此基础上,我们还可以通过集成式的冷却水道,进一步集成小三电和油泵的控制部分,实现不低于80千瓦每升的功率密度。
通过这个逻辑融合,我们可以把小三电和油泵的控制和主驱动电机融合进来,进一步提高系统的集成度。润滑部分,我们采用了可变液面和分层润滑技术,集油盒在高速运行的时候集油,既降低了液位、避免搅油损失,又可以通过油道给轴承提供润滑。
我们还采用串并联油路的精确润滑技术,通过主动泵的润滑,可以不受限于系统的工况,总成不论是在正转、反转,甚至左右倾斜的情况下都能够精确的把润滑油送到其所需要的地方。我们采用了智能流量控制技术,根据系统的各种状态,如转速、功率,调节电子泵运行情况,能够把系统的温度和效率都控制在合理水平。
在提高功率密度的过程中,结构设计和热设计常常是矛盾的。对此,我们建立了一个涵盖电机、电控和减速器的热反拱平台,在该平台上通过离子法和多相流的CFD仿真技术,能够精确预测流体的散热能力,评估冷却方案的设计效果。
仿真准不准,不仅取决于建模的水平,还要通过实验进行校正和验证。我们建立了行业领先的电驱动总成热测试平台,通过无线遥测实现了转子温度的测量。之前在转子温度测量时,要么在静态的状况下放测温线进去,或在运行的状态下,用开洞或通过布置测温纸等方法,但这些方法在深度集成的油冷架构下难以实现。对此,我们用了无线遥测技术,通过无线传输将能量输送到转子,并将转子上的测温信号再传输出来,这个测试相当稳定和精确。
在此基础上,我们通过整车动力学仿真和下标测试,识别了非常丰富的热测试的运行工况,建立了丰富的总成温升数据库。结合仿真平台,实现了对于总成热稳定边界的精确估测,其中转子温升的估测误差不超过5摄氏度,甚至可以取消电机的温度传感器,通过在线温度的估算实现电机热控制。
项目最开始时,我们计划采用业内比较成熟的电子喷油环结构,但由于为我们的仿真能力非常强,很快就实现了方案的迭代。一开始采用多种冲片旋转叠加构成电子外表面油道的方式,这种方式能让冷却油通过电子外表面的油道,实现喷淋冷却。后来我们发现仅仅用一种冲片就可以把它继续优化。
我们在此基础上进一步优化,从电子表面开槽进一步升级成电子铁芯内部的油道设计,这样可以进一步优化定子铁芯和外部壳体的接触。转子方面,采用内置冷却的方案,通过空心轴、隔磁板和转子铁芯内部构成一个油道,实现高水平的冷却。最终,我们的电机温升比起第一代的方案降低了14度,持续功率提升了20%。
高舒适性层面,电驱动总成的舒适性主要表现为NVH的特性。很多人都认为NVH是玄学,之前我们也是这么认为的,当时工作的重心主要在测试和整改上面,出现问题再去分析原因、整改。随着开发周期缩短、质量成本上升,这种方法不再适用。我们集中力量攻关,实现了NVH开发工作的前置。当前的开发流程中,我们已经能够实现对整车目标进行零部件级别的分解,并通过仿真和测试进行快速迭代优化。
仿真方面,我们建立了一个涵盖电机、电控、轴齿、电驱动总成的NVH仿真平台,在这个平台中首先通过对电机和电控建模,仿真电机的电磁力,并分析电磁力在时间和空间维度的表现。同时,我们建立了轴齿模型,实现了对于轴齿啮合力的计算和分析,并且可以将它们映射到电机的定转子。针对外轴上传来的外部冲击,我们建立了传动链间隙情况的模型,进一步提高了轴齿载荷的分析精度。
我们把上述因素共同作用在总成的结构模型上进行仿真,得到的结果就可以提示我们,哪些地方是声音辐射的主要区域,哪些地方需要进行结构加强。再结合多目标参数的优化技术,就可以得到总成结构的优化方案,包括轴齿方案,声学包裹方案,甚至能够指导电控软件进行工作。
NVH的仿真也需要靠实验进行检验和校正,我们建立了一个电驱动总成的NVH实验平台,可以实现电驱动总成的台模NVH测试、模态测试和总成ODS测试,通过整车NVH评测进行最终的闭环。
大家认为NVH是玄学的另一个原因在于状态的不确定性。比如命名开发的时候样机状态非常好,但到了量产就会有问题。针对这种问题,我们正在尝试把总成测试结果和零部件制造参数联系起来,通过大数据分析其中的联系,再进一步优化设计和轴承控制。在这些仿真和测试平台帮助下,我们很快实现了全方位的NVH优化。
电磁方面,通过结构和电磁方案的协同优化,针对主阶次进行了优化,相关阶次噪音能降低50%以上。控制方面,我们采用了开环和闭环结合的斜部注入方案,可以实现常用转速的全覆盖。针对开关噪声,采用随机载频的方案,相关噪音可以降低10-15dB。我们通过优化机械盒的结构,改善噪声,降低低频道声,所有措施加起来实现了主阶次一米声压级低于68dB,达到了行业领先水平。
新技术探索
技术进步是无止境的。除了之前在量产中用的技术外,我们正在探索新技术。针对客户系统效率极致追求的场景,我们开发了输出断开的手段,探索了各种方案,有些量产的基础好一些,有些能从外面找到现成的供应商,目前还在进行优化的方案选择。
高功率密度扩展方面,我们正在探索异构铁芯技术,通过提升电机转速,进一步提升功率密度。我们采用960兆帕的硅钢,可以在不依赖碳纤维转子包裹的情况下,把电机的最高转速提升到24000转,同时将电机的定子分瓣,采用高性能的硅钢片。在这些技术的帮助下,我们可以把最高效率提升0.2%,功率密度提升10%。
电驱动总成的安全主要靠电控,我们目前已经获得了单电机控制器功能安全C级别的产品认证,接下来会进一步探索在小三电融合控制架构下面的功能安全问题。在功能安全架构下,大部分场景都要求实现安全停车,但仅实现安全停车是不够的,我们还要做到容错运行和诊断预警。针对传感器容错控制的问题,我们开发了无位置传感器的控制算法,可以在常用的工况下做到驾驶员无感切换,避免动力中断。
针对主要功率器件的寿命问题,我们正在探索基于功率器件结温和容值预测的预警机制。针对轴电压造成的轴承电腐蚀问题,正在采用基于陶瓷球和导电刷的方案。我们也在研究通过调制策略的优化,降低周电压,延长轴承寿命,探索能否进一步取消陶瓷轴承。
智新科技介绍
智新科技前身是东风电动车辆股份有限公司,这家公司成立于2001年,可以说是中国新能源汽车事业真正起步的地方,因为当年国家863重大专项就落在这里。2022年,原东风雷诺和原智新科技进行战略整合,新公司名称采用了智新科技。2023年,东风乘用车的业务并入智新科技。现在我们公司的架构和弗迪动力非常相似,可以提供纯电、混动、增程、传统动力全部内置化研发和设计能力。
我们的动力总成有一个统一名字,叫马赫动力。马赫动力品牌覆盖油动、混动和电动的全部领域。马赫这个名字的含义代表动力澎湃、超强驾控、高效环保,给用户带来愉悦的驾乘体验。我们的产品平台包括马赫G、传统动力总成、马赫MHD混动动力总成、马赫E、纯电力总成。
近5年,我们已经累计向客户提供超100万套动力总成,到今年年底或许可以超过200万套。
东方风起,科技跃迁,智新科技愿意与上下游共同发展,全力打造创新发展新格局。
(以上内容来自智新科技股份有限公司研发中心电控开发专业总师王闻宇于2024年10月24日-25日在第十二届汽车与环境创新论坛发表的《新一代新能源驱动系统开发技术及应用》主题演讲。)
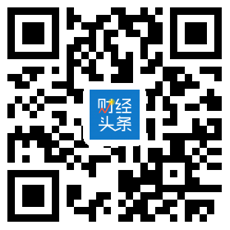
4000520066 欢迎批评指正
All Rights Reserved 新浪公司 版权所有