一、意识引导、培训先行
精益生产方式十分强调员工的作用,它认为如果企业在实施精益生产过程中只把注意力集中在精益生产本身的方法上,那么由此带来的变化将是暂时的,一旦推动精益生产的顾问或经理离去活动也就停止了,要想获得长期成功,必须着眼于全体员工,让他们成为实施的主体,从破除传统的管理思想,变革他们的工作方法,改变他们的工作习惯,提高全体员工的质量意识、专业技术管理知识、操作技能水平、工作责任和积极性,为搞好精益生产提供根本保证。
精益生产方式与传统计划推进方式是两种截然不同的生产管理模式,涉及到企业管理的方方面面,实质上是一种管理变革,势必会冲击现有的工作、思维方式及某些人或集团的既得利益。为此,公司在内部开展广泛的精益思想的宣传和学习活动,通过各部门每周例会形成制度化学习精益生产方式,组织各部门科组长等现场管理人员集中学习精益生产业务知识,来促进员工思想观念的转变。
二、确立组织、精心计划
公司在开始实施精益生产时,建立了精益生产组织。在实施精益生产前期是公司的辅助生产组织。这个生产组织包括一个“精益生产指导委员会”,和两个执行团队:“物料团队”和“工序团队”。
精益生产指导委员会核心成员包括总经理、生产总监、技术总监、生产工程部、生产部、质保部、人力资源部、操作员工代表、信息系统人员等主要负责人,其主要职责包括从参与实施团队的部门调动人力资源;主持定期会议来审核实施的进展,要评审活动项目的状况和精益生产管理方法的运行情况,按照由精益生产实施团队提出的修改意见来理解和协调现行的经营惯例;监督计划中重大事件的里程碑,并为保持精益生产实施的进展而确定优先次序;确保为规定的供应品、看板物料和逐渐增长的机器资源和劳动力资源提供资金;制定一套联系和宣传策略,以保证全部员工、顾客和所有供应商都会受到实施精益生产项目的预期好处。在各种需要已经明确的情况下,制定必要的培训计划,为计划提供资金并配备人员;保证达到公司既定的经营目标。
三、 现场改善、稳固基础
6S现场管理
公司在实施精益生产前期狠抓6S现场管理,深刻理解6S管理精髓。整理在于组织化,为使工作能充分发挥应有的机能应具有哪些必备的物品及应有的流程;整顿在于考虑流程的合理化,具体分析每个产品生产流程是否合理;清扫的精髓在于逐点的检查确认,以发现问题点;清洁在于彻底改善,在问题点发现后,若不彻底加以解决,会养成忽视、敷衍的心态;素养在于训练与纪律,员工接受严格训练,最终严守纪律。安全在于尊重生命,排除危险,预知不安全人为、物为因素并彻底改善。真正实现6S管理效果,为实施精益生产奠定基础。
生产线布置
基于精益思想的生产线布置要有这样几个特征,物流流动的一个流及同期化,员工的多工程化及多能工化,设备的整流化。公司运用ABC分类法对公司所有客户进行管理。对于长期客户、产品需求量大、销售额占比重高的A类客户,进行独立拉式生产线布置,充分保障重要产品交货期和质量。对于C类客户,考虑到压铸行业特点,换模时间长,此类客户仍沿用传统的批量式生产。
设备预防维修管理
精益生产一件流快速拉动需要全面实施设备预防维修计划(TPM)来保障,通过OEE(整体设备效率)考核。考虑到压铸行业模具容易出现故障,为此公司组建专业的设备维修部,制定公司所有模具和机器设备预防性维修计划,对所有机器和模具定期检查维修。并根据月度生产计划,对要启用的机器和模具全检,保证把故障排除在生产之前,避免因模具或机器影响交货期。
设备布置
要充分考虑各生产环节之间的关系,在实现产能要求的基础上,尽量做到各设备单元产能均衡,体现精益一个流的思想。公司通过机器重新布置,破除孤岛式生产。如打破后加工部、自动机加部和五金部界限,并根据生产工序需要,编制成单元式生产线。加速产品流转速度,有效消减工序间在制品数量。
四、循序渐进、由神到形
精益生产方式的实施是一个逐步推进的过程,对于一般的企业可以采用精益管理的理念进行组织生产。企业进行组织实施精益管理时不一定要照搬丰田生产的模式,应该根据本企业的具体情况,以精益管理的理念和方法,一步一步的进行推进,尽量以最小的整改成本取得最大的效果,在这里就需要仔细思考本公司的具体条件,又有哪些方法措施是适合本公司的。
公司作为压铸行业的代表,结合自己实际,要考虑到大型的压铸机体积大,搬运不方便,而且作业时对其他机器设备影响较大;喷涂车间需要封闭的环境作业,容易对其他车间造成工作环境影响等情况。公司实施精益生产改造时,只采用需求拉动式生产系统,对部分车间单元式生产线设计,达到了精益生产的效果。
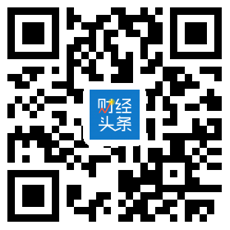
4000520066 欢迎批评指正
All Rights Reserved 新浪公司 版权所有