以碳化硅、氮化镓为代表的宽禁带化合物半导体(又称“第三代半导体”)是战略性新兴产业的核心材料。相较于第一代和第二代半导体材料,具有高击穿电场、高饱和电子速度、高热导率、高电子密度等显著优势,被广泛应用于新能源汽车/充电桩、光伏发电、智能电网、轨道交通、航空航天等领域,被视为推动能源、交通、信息和国防产业发展的核心技术。
碳化硅半导体器件,以其耐高压、耐高温、能量损耗低、功率密度高等绝对优势,在新能源汽车、充电设备、便携式电源、通信设备、机械臂和飞行器等多个高附加值工业领域发挥着重要作用。当下热门概念股“人形机器人”、“低空经济”、“光伏”、“新能源”等,都与碳化硅材料大量应用密切相关。
碳化硅器件“上车”加快
随着新能源汽车对功率平台的要求从600V提升到800V,甚至达到1200V,功率芯片的性能需求也在不断提高。这些功率器件主要被应用于新能源车的主驱逆变器、车载充电器、DC/DC转换器等关键电驱电控部件。尽管SiC MOSFET价格比Si IGBT价格更高,但碳化硅功率器件在耐压水平、开关损耗以及耐高温性方面具备明显优势,新能源汽车已成为碳化硅功率器件最主要的市场。
在主驱逆变器、车载充电器、DC/DC转换器等关键电驱电控部件中使用碳化硅器件可带来以下优势:
① 提升效率
低开关损耗:在高频切换过程中,碳化硅器件的损耗远低于传统的硅器件,这意味着在电能转换时的效率更高,尤其是在高频应用中。
低导通损耗:碳化硅器件的导通电阻小于传统硅器件,这进一步提高了效率。
② 降低能耗与热管理需求
优异的热性能:在高温条件下,碳化硅器件的性能损耗小于传统硅器件,简化了冷却系统的复杂性并降低了成本。
减少能量损失:提高效率直接减少能量损耗,使充电过程中的能量转换更加高效。
③增强系统可靠性
高温稳定性:在高温环境下,碳化硅器件展现出更好的稳定性,增强了系统的可靠性和寿命。
耐高压性能:碳化硅器件能够承受更高的电压,提供了更好的安全性。
④支持高性能系统设计
小型化设计:由于碳化硅器件允许更高频率的操作,使得变压器和其他电磁元件能够更小型化,减少了整个系统的体积和重量。
灵活的系统集成:碳化硅的性能优势使得双向OBC设计可以更加灵活,有助于在电动车辆中更有效地集成。
在今年4月举办的北京车展上,众多车企披露碳化硅技术的新进展。岚图汽车推出了自主研发的最新一代岚海动力系统,该系统配备了800V高效碳化硅电驱动系统;蔚来汽车展示了其自研的1200V碳化硅功率模块;吉利汽车则展出了其碳化硅混合驱动集成的关键技术。
小米汽车宣布,SU7系列将全面采用碳化硅高压平台,并且所有驱动电机都将使用碳化硅功率模块。士兰微也透露,汽车级碳化硅功率产品的需求量正在迅速增长,预计到5月,公司的碳化硅主驱动模块的装车规模将超过8000辆,而6月将超过2万辆。
8英寸碳化硅晶圆逐渐成为行业趋势
高成本一直是碳化硅器件被吐槽的弊病,这主要是因为在生产过程中,碳化硅单晶的生产周期长、环境要求严格、良率低等问题。特别是在碳化硅衬底的生长过程中,需要在高温和真空环境中进行,对温度场的稳定性要求极高,而且其生长速度与硅材料相比有着数量级的差异。因此,碳化硅衬底的生产技术难度大,良率不高,这直接导致了碳化硅衬底价格高、产能低的问题。
业内人士指出,目前碳化硅器件的价格通常是硅器件的4到5倍,行业的目标是将碳化硅器件的成本降低到硅器件的2.5倍甚至更低。
为了优化碳化硅器件的产能和成本,最佳途径是将芯片制造从6英寸晶圆转移到8英寸晶圆。此外,提高良率,并将器件类型从平面型转变为沟槽型,有助于整体上降低碳化硅的成本。一般来说,衬底尺寸越大,每片衬底可生产的芯片数量就越多,从而降低了单个芯片的成本。与6英寸衬底相比,在相同条件下,8英寸衬底切割出的芯片数量增加了近90%。相较于6英寸衬底,8英寸单片衬底制备的器件成本降低了约30%。
目前,多家上市公司正在加快布局8英寸碳化硅产能。例如,士兰微在5月21日宣布,公司与厦门半导体投资集团有限公司、厦门新翼科技实业有限公司签署《投资合作协议》,计划在厦门市海沧区建立一条以SiC-MOSEFET为主要产品的8英寸碳化硅功率器件芯片制造生产线,其产能规模将达到每月6万片。另外,三安光电也表示,湖南三安工厂正在扩大产能,将全面采用国际领先的8英寸生产设备和工艺,并计划在今年第三季度开始生产,达到年产48万片的规模。公司的8英寸碳化硅衬底外延工艺已完成调试,相关样品已送至主要的海外客户进行验证。
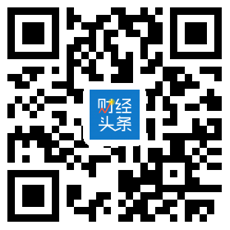
4000520066 欢迎批评指正
All Rights Reserved 新浪公司 版权所有