中国经营报《等深线》记者 李哲 北京报道
“自从进了项目组,压力就一直比较大。”回忆起15年前,刚参与首套国产乙烯装置设计工作时,中国寰球工程有限公司(以下简称“寰球公司”)北京分公司工艺部主任孙长庚提到最多的一个词便是压力。
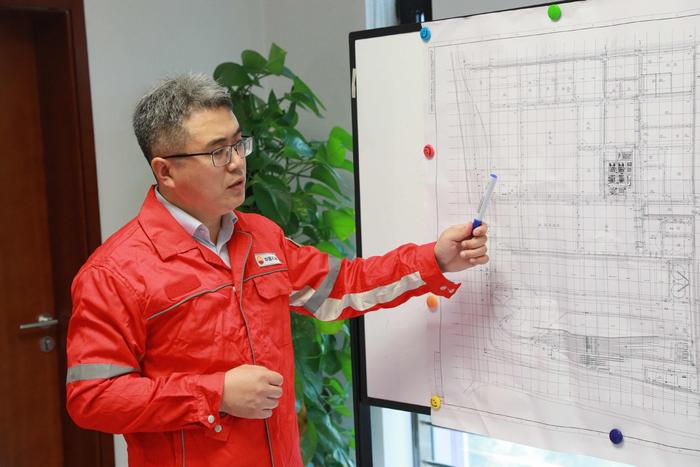
作为现代石化行业的“桥梁”,乙烯的原料广、副产品多,同时性能活泼、衍生产品丰富,可以用于生产衣食住行的日常生活用品,以及飞机、高铁等零部件。乙烯及其衍生品占全部石化产品的75%以上。因此,国际上将乙烯产量作为衡量一个国家石油化工发展水平的重要标志。
2008年,我国已成为世界第二大乙烯消费国,但60%以上的乙烯产品需要依靠进口。当年,中国石油设立乙烯国产化重大科技专项,作为中国石油全资子公司,这副担子便落在了孙长庚所在的寰球公司。
十五年后,总投资654亿元的中国石油广东石化一体化项目在2023年2月27日实现一次开车成功,进入全面生产阶段。其核心装置120万吨/年乙烯装置同样出自孙长庚的设计团队。
作为寰球公司核心设计团队的一员,孙长庚在这十五年间见证了国产乙烯零的突破,这让我国成为了世界上第四个掌握乙烯技术的国家。
时尚“奶奶灰”
初见孙长庚,引人注目的除了闪烁着光芒的眼神,还有一头醒目的“奶奶灰”,这与他43岁的年龄似乎并不相衬。
“最初参与国产乙烯项目设计的时候,心里没有底,我都不知道自己能不能做出来。”回忆起参与乙烯国产化设计之时,孙长庚感叹道,“感觉特别紧张,压力特别大,睡不着觉。只有一个问题解决以后,才会感觉到困。”
让孙长庚倍感压力的便是乙烯。这个似乎与普通人生活相距很远的物质,对我国化工产业乃至老百姓的日常生活息息相关。
“我们知道做馒头、包子、面条要用面粉。在石化领域,乙烯就好比面粉,它的衍生品覆盖工业、农业、国防、交通和人民生活衣食住行的方方面面,地位和钢铁同样重要。”孙长庚向记者说道。

如今,现代化工经过长期的发展,乙烯逐渐扮演起桥梁作用。孙长庚表示:“通过乙烯可以把整个石油化工产业联系起来。”这进一步巩固了乙烯在现代化工产业中的核心地位。据统计,乙烯衍生品在化工产品中的占比可以达到75%。
特别是石脑油制乙烯的过程,其出产的产品非常丰富。包括氢气、乙烯、丙烯、丁二烯、汽油等一系列产品。因此,乙烯可以延伸出很多产业。建设一套乙烯装置,就能形成一个庞大的产业链。
我国的乙烯工业始于1962年。彼时,兰州石化500吨/年乙烯装置建成投产。此后,经过长期发展,我国的乙烯产能不断扩大,2009年前后,我国乙烯产能已经达到世界第二,但大而不强的问题依然存在,核心技术掌握在国外专利商手中。
2008年,中国石油决定打破乙烯技术引进惯例,设立乙烯重大科技专项,以大庆石化新建的60万吨/年乙烯装置为依托,实施乙烯国产化战略。这一设计任务由孙长庚所在的寰球公司承担。
寰球公司在乙烯装置有着深厚的积淀。20世纪60年代参与了早期裂解炉的设计,70年代参与大庆首套乙烯装置的建设,与多家专利商进行乙烯装置引进谈判,并派人赴国外考察学习乙烯工艺技术。90年代后期到世纪之交,国内外乙烯工业发展迅速,寰球公司的乙烯设计项目接踵而来,为其积累了大量宝贵经验。在寰球公司发展历程中,逐渐涌现出黄文、张来勇、杨庆兰等探路先锋,一代代寰球人的不断突破,带领我国乙烯产业,走到了国产化的大门前。
“我2004年底来到公司,参与了一个乙烯装置全过程的工程设计、现场设计代表和开车服务,可能我对乙烯技术追根问底、经常提问题的工作态度引起了领导的关注,2008年被吸收到乙烯技术开发项目组,那时候我对工艺包一切全都未知。”孙长庚回忆道。
当时,孙长庚作为核心人员参加了乙烯裂解炉、分离工艺技术开发和工程技术开发的全部课题,并担任其中一个课题的副课题长。沿着前辈的足迹,孙长庚走上了他的舞台。
“百万吨乙烯装置加上下游配套装置和公用工程其投资达到数百亿元。如果乙烯装置出了错,配套的那些装置也白建了。”孙长庚感慨道。
据了解,一套百万吨乙烯由五六百台/套设备构成,每台设备至少也受到近10个关键工艺参数影响,搭建一个物料和热量平衡计算模型就需多达800多个模块,一次计算生成的报告打印出来超过8000页。面对复杂的乙烯装置,压力可想而知。
石脑油制乙烯装置的副产品多,下游延伸空间很大,可覆盖多个方向的需求,因此,一套大乙烯装置落地,可通过多个产品带动当地经济发展。而这些产品的“龙头”便是乙烯装置。
那段时间,身边的人都觉得他“魔怔”了,吃饭的时候经常一个人坐在角落自言自语,走路的时候低着头嘴里念念有词,洗澡经常能洗1个小时……在长时间高压和用脑的情况下,不到半年时间,孙长庚这个技术专家便在那时走起了“时尚路线”,一头乌黑的头发变为花白,“奶奶灰”一直陪伴着他。
从零起步
谈及乙烯装置,业内人士曾将其复杂程度同核电相提并论。
从化学角度来看,乙烯是结构最简单的烯烃。而生产乙烯的装置却并不像其分子结构那样简单。据了解,一套百万吨乙烯装置占地可达10万平方米,面积相当于14个标准足球场。装置由数百台设备构成,连接管线加起来超过200多公里。
乙烯产品线的复杂还不止于此。孙长庚说道:“乙烯装置生产特点之一是原料成分复杂,可以说世界上没有任何两套装置原料是一样的。”
长期以来,石脑油制乙烯是乙烯生产的主要途径。孙长庚参与设计的第一套乙烯装置同样采用石脑油作为原材料。这种由原油加工生产得到的原材料,因为全球各地的原油成分存在差异,加工路线有所区别,导致其组分差异比较大。
乙烯产业诞生之初,国外公司通过逐步探索,一级一级地逐渐放大,经历了从实验室到实验工厂再到产品线的过程。
然而,2008年孙长庚及其团队接到第一套国产乙烯设计任务之时,无论从时间还是场地方面考虑,都不可能再重新经历这一过程。
与此同时,由于石脑油制乙烯下游生产线长的特点,乙烯装置几乎囊括了所有化工过程中的单元操作类型,牵一发而动全身。每一项参数的微小变化,逐级放大后传递到下游,便可能造成很大偏差。
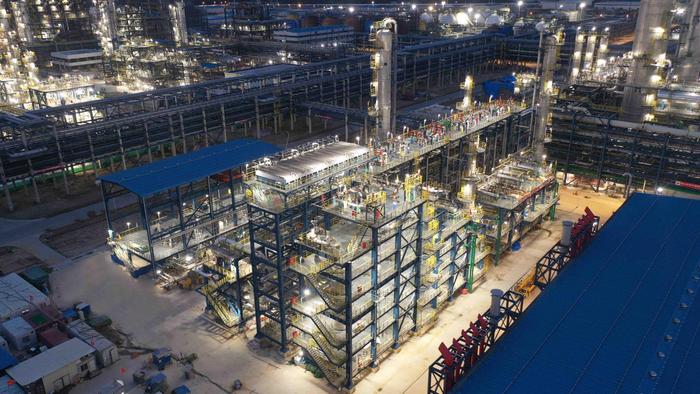
孙长庚举了一个例子:“在设计的过程中,需要预测组分,前面的偏差会影响到后面产品的分离,随着分离流程的进行这些偏差会被放大,这个偏差怎么控制,怎么认识这些偏差,用什么方法尽量来缩小这些偏差,如果没有经验,这是一个很难想象的过程。特别是对乙烯这个长流程的装置。”
“当时我面临最大的问题是如何整合系统。”孙长庚回忆称,“第一感觉是无从下手。这是一个系统问题,并且是一个多维度的状态,各系统、各参数之间又互相制约。像是一团麻,我必须把这些关系全部理顺。”
孙长庚和他的同事就这样,迈出了乙烯国产化设计的第一步。
寻找切入点
“起初我的想法是做到尽善尽美。把每一个变量都控制在一个精准的范围内。但实际操作过程中发现这是很困难的。”孙长庚举了一个例子:“比如,过程中某个换热器进出口两侧的温差只有1.5℃。如果将温差调整0.5℃或1℃,那么换热面积可能会改变30%以上。但是在裂解炉炉膛,里面的温度高达一千三四百摄氏度,一两度的温差可能影响没那么大。”
但是,面对如此庞大的体系,如何把握这个度,当时的孙长庚是理解不了的。“这就如同设计一辆车,但不懂原理,这样造出来的车是否能上路不知道,如果出现问题想要解决就更一无所知了。”孙长庚说道。
对于当时没有明确方向的孙长庚而言,在和同事的交流过程则显得更加六神无主。“当时的工作氛围让我印象很深,大家没有专家的架子,特别是一些老同志,大家都是在平等地讨论问题。但是因为我起初并没有建立起自己的认知体系,各种不同的声音交织在一块,我感觉每个人说的似乎都有道理。”
“根据直觉在把模型搭起来以后,我发现已经走进了死胡同。”即便如今,回忆起当时的场景,孙长庚的表情中仍流露出失望的情绪。
在被“迷雾”笼罩的时候,孙长庚最终还是在团队的力量中寻找到了支撑。
“团队人员背对背解决一个问题,各自拿出自己的方案,然后讨论形成最终结果。通过大量反复的计算、对比、再计算、再对比等重复性工作,最终我们找到最佳解决方案。大庆装置开车前,我总是担心我们的计算准确性,经过装置运行证明,我们集体的智慧还是经受住了考验。”孙长庚回忆道。
置身于团队的思想碰撞中,孙长庚的认知渐渐清晰起来。
“这个过程中有的数据偏差特别大,我就思考到底是哪儿出现了问题,前后花了几个月的时间来计算、分析,这相当于理解的过程,对我来说这是一个很大的帮助。”孙长庚回忆道。
这样的一个切入点,让孙长庚豁然开朗。“这个过程让我逐渐理解了那些内容。在脑子里建立了一个相对完整的体系,对我来说也增加了不少信心。”

确定了正确方向为其后续的工作做了一个很好的铺垫。“我当时建立的模型有50多个组份,还要包括温度、压力、密度等一系列参数。那段时间,我几乎可以全部记住。只要指出流程的某一个环节,我大概都能知道这里面组成是什么,里面的物性是什么,温度压力是多少。”孙长庚回忆道。
孙长庚表示:“通过我的经历,现在我一直和同事说,一定要形成自己的想法和认识,哪怕当时的认识是片面的,也一定要有自己的判断,因为认识可以在讨论中发现和修正。没有一个特别自信或明晰的判断的话,很难把这件事做好,因为你对它是不了解的。”
从40天到1分钟
建立了自己体系的孙长庚随后不断完善模型,逐渐加快了设计的步伐。
孙长庚用乙烯装置中的燃烧过程举了一个例子:“燃烧是生活中司空见惯的现象,但是在化工工艺过程中,燃烧是一个过程。如何把这个过程通过模型,用数字的方式体现出来,就是我们需要探寻的。”
“裂解炉炉膛内温度可以达到1400℃。上世纪七八十年代在做反应设计的时候,普遍会把炉膛里面的温度当作唯一的设计出发点,但事实却并非如此。”孙长庚说道。
“炉膛中燃烧实际是一个复杂的过程。我们必须自己编程,把炉膛的燃烧和传热过程描述出来。”孙长庚解释道,“燃料组成、温度、压力、流量等因素决定了燃烧器的火焰高度。火焰高度不同,最高点的温度就不同。此外,传热过程中不同温度下的传热速率也不同。燃烧过程更是辐射传热、对流传热等几种传热方式的组合,不同区域它们的贡献比例也在变化。”
因此,计算结果的准确与否,最初基本需要通过经验和已建装置的运行情况来判断。
“通过流程软件,设置不同的参数进行模拟,最初做一次需要40天时间。这个过程漫长而且数据量很大,还需要考虑计算结果的准确性。”孙长庚回忆道,“我们逐渐认识到,炉膛内温度分布更像一个三维立体结构,每个地方都有所不同。为了准确表述温度,我们从影响温度的因素着手逐个分析,比如,烟气流量的影响、炉膛表面反射的影响,等等。在这个过程中我们花了大量的时间。”
随着对燃烧过程和工艺过程结合理解的加深,我们找出关键点,并且总结成一套自己的简化模型,现在再算一次,只需要不到1分钟就可以完成。
“我们从最基础的入手,先认识一个问题,把这个问题分解,再把问题提炼出来,然后形成公式,通过改变输入条件,得出来的结果跟我们知道的现实尽管并非一模一样,但一般不会有较大的偏差。如果模型输出结果和预想的差别很远,或者跟实际差别很远,说明模型还不完善,甚至是错的,需要调整。在整个设计过程中,这样的模型有很多。随着认识的加深,在做设计的时候,逐渐把握住主要因素,对影响因素小的环节进行简化,从而形成规律。”孙长庚解释道。
最终,历经近五年的艰苦攻关,2012年10月,国产乙烯装置在大庆石化开车成功,比原计划提前一年,各项指标均达到国际先进水平,一些指标甚至超过了国外技术。至此,我国一举打破了乙烯国产化壁垒,成为世界上第四个掌握乙烯技术的国家,中国石油也因此成为世界上第六家乙烯专利商。
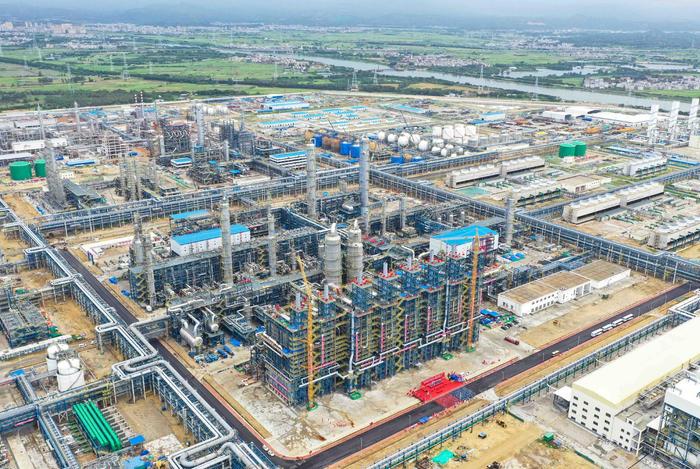
使用国产专利技术后,每套装置(以100万吨/年乙烯为例)能为企业节省2~3亿元的投资费用。此外,通过先进技术的应用(如:强化传热炉管和乙烯回收先进技术),也为企业提供了更强的市场竞争力。
2015年,乙烯成套技术获中国石油科学技术进步特等奖,2016年大型乙烯装置成套工艺技术获得2016年国家科技进步二等奖。
目前,国产自有乙烯成套技术已被推广到中国石油系统内外等9家企业的十几套乙烯装置中应用;乙烯特色节能技术在4家企业使用,装置规模从60万吨/年到140万吨/年乙烯,原料品种覆盖了天然气分离、石油炼制、煤基合成等领域,大庆石化(60万吨/年乙烯装置)、国能宁煤(100万吨/年烯烃)等项目的运行数据表明,国产自有乙烯技术在裂解炉的产品收率、操作周期、热效率以及装置的乙烯收率、综合能耗等各方面指标均达到国际先进水平,部分指标达到了领先水平。
未雨绸缪
就在孙长庚和他的同事们完成国产乙烯设计工作同年,大洋彼岸掀起了一场页岩气革命。
2012年,全球以乙烷、丙烷等轻烃为原料的乙烯产量首次超过以石脑油为原料的产量。页岩气革命为北美化工业提供了大量廉价乙烷,这对全球石油化工行业产生了重大影响。
“乙烷制乙烯投资少,收益高,运营成本低,这个特点特别明显,所以美国、中东新建的装置中,乙烷原料占了相当大的比重。”孙长庚解释道,“当时,塔里木项目还在酝酿期,有一些国外的拥有乙烷原料的业主来找我们咨询,我们认为,虽然国内乙烷原料少,当时用不上,但乙烷制乙烯技术一定有用,于是就开发了乙烷裂解炉,然后塔里木和长庆两套乙烷制乙烯项目开始上马。可以说这一次是未雨绸缪了。”
对于我国而言,乙烯的需求量连年提升,带动产能迅速增长,面对轻烃资源优势和日益严峻的竞争形势,降低乙烯原料成本势在必行。
同时,随着世界能源消费结构的逐渐变化,大部分炼厂都在考虑由生产汽柴油为主向多生产化工原料方向转型,石油烃蒸汽裂解制乙烯技术作为“减油增化”最重要的桥梁技术,成为相关企业转型升级的首选。
为顺应乙烯工业发展新趋势,增强炼化企业竞争力,巩固中国石油在大乙烯技术方面的优势,中国石油于2016年启动二期乙烯重大专项“大型乙烯关键技术升级与工业应用”的立项工作,并于2016年底正式立项。这副担子最终又落在了寰球公司和孙长庚所在的团队肩上。
“做乙烷制乙烯的时候,压力就小多了,从某种程度上来说,可以说是一个简化版。”孙长庚说道,“这个简化不是说把部分内容简单删掉了以后的简化,而是通过新的工艺路线的开发,缩短了工艺流程,减少了设备数量。”
孙长庚口中的轻松,更多的是一种心态上的变化。“就像我们此前设计轿车,现在要设计一辆卡车。那么我们只需要根据卡车的特点做出相应的设计,而汽车的原理我们已经有了相应的体系。”孙长庚说道,“我们当时想,肯定能做出来。做乙烷制乙烯项目的时候,我的角色发生了一些变化,从做模型转变为校审和乙烷裂解的开发,同上一次几乎无法入睡相比,我更多的时间和精力是校审和问题讨论,可以说轻松了很多。”
2019年,中国石油上马兰州石化长庆、独山子石化塔里木两个乙烷制乙烯工程。寰球公司采用总承包模式进行项目设计建设。2021年8月,经过两年的设计与建设,两个项目先后提前投产。
孙长庚和同事们开发的乙烷制乙烯技术工艺包,使得乙烯收率由液体原料的30%左右提高到80%,成本降低约30%,在关键技术上达到世界先进水平,填补了国内纯乙烷裂解制乙烯成套技术的空白。
对于如今的孙长庚来说,其思考的已经不局限于项目本身。“乙烷制乙烯虽然有着诸多优点,但其短板同样明显。由于国内开采的天然气中乙烷资源较少,如果乙烷来源无法解决,那么乙烷制乙烯项目发展可能还是受限。同时,与石脑油制乙烯不同,乙烷制乙烯的产品组成相对简单,下游除了氢气以外,可以延伸加工的只有乙烯,这就造成其产业链单一。”
但纵观全球乙烯市场,乙烷制乙烯工艺包仍有其用武之地。“乙烷制乙烯有其明显的优点。这个工艺包也许会成为中国石油未来走向海外的一个‘敲门砖’,去打开一些海外市场。”孙长庚说道。
添一抹绿色
当时代的脚步走进2023年,现代化工的脚步与碳中和同频成为未来发展的重要方向。作为碳减排大户,石化行业正在经历新一轮的转型升级。
2021年5月,中央层面成立了碳达峰碳中和工作领导小组,随后,围绕碳达峰、碳中和的“1+N”政策体系逐渐形成,把碳达峰、碳中和逐渐纳入我国经济社会发展全局之中。
2022年8月,工业和信息化部、发展改革委等多部委联合发布的《关于“十四五”推动石化化工行业高质量发展的指导意见》提出,到2025年,石化行业基本形成自主创新能力强、结构布局合理、绿色安全低碳的高质量发展格局,高端产品保障能力大幅提高,核心竞争能力明显增强,高水平自立自强迈出坚实步伐。并重点提到,发展清洁生产,构建全生命周期绿色制造体系。
实现全生命周期清洁生产,这就要求从设计开始,便着重考虑到绿色发展理念。
孙长庚及其团队在乙烷制乙烯项目设计之初便充分考虑了环保要求,开发了裂解炉烟气脱硝技术,并首次使用中国石油自主开发的脱硝催化剂,使裂解炉中排放的氮氧化物浓度远优于国家标准,比现有常规乙烯装置降低70%,二氧化碳排放量、年综合能耗均可达到世界先进水平。
同时,上述项目的裂解炉排放源均安装了在线监测设施,可保证CEMS在线监测烟气,保证装置在正常、清焦、热备等各工况下均实现达标排放,厂界上下风向和厂区内安装多套无组织排放在线监测设施,实现无异味工厂目标。
当前,氢能作为清洁的二次能源的代表,正随着碳中和的推进冉冉升起。兰州石化长庆乙烷制乙烯项目,80万吨/年乙烯产量理论上可产出5万多吨99.9%纯度氢气,为氢能的利用提供了极大的支持。
此外,塔里木乙烯项目的废碱处理采用寰球公司开发的先进湿式高温氧化工艺,废碱液经过氧化处理后,结合蒸发结晶技术,实现了废水近零排放。
2023年2月27日,总投资654亿元的中国石油广东石化一体化项目实现一次开车成功,进入全面生产阶段。这个中国石油一次性投资规模最大的炼化项目,配套年产120万吨乙烯装置。这套装置同样出自孙长庚之手。
作为广东石化一体化项目的核心环节,120万吨/年乙烯装置的建设应用了中国石油寰球工程重大专项《大型乙烯装置工业化成套技术开发》的研发成果,是目前国内自主技术最大规模国产化乙烯装置。其中运用的“乙烯裂解炉高效节能技术”,增加超高压蒸汽产量20%,裂解炉热效率高达95%。
谈到广东项目,孙长庚举了一个例子:“当时做了很长时间的原料优化,到最后优化的就是能耗,如何把能耗降下来,把乙烯收率提上去。”
“随着能源转型的加速推进,油气资源燃料属性逐步让位于原料属性,减油增化、减油增特、减油增绿将成为主流,基于这样的行业发展趋势,我们开发百万吨原油裂解制烯烃技术,可以绕过炼油流程,直接加工原油,加工流程短、投资少、化学品率高,可以最大化地提高资源利用率;同时,为了降低装置的碳排放,我们一直在提高炼化装置电气化率,全力走好探索之路。”
征途漫漫。如今思考更多、担子更重的孙长庚,还未停下脚步。“按照我们现在的理解,乙烯技术是一个面,我们正从其中一点逐渐外扩,不断去接近这个面。”
(中国寰球工程有限公司王利对本文亦有贡献)
(编辑:吴可仲 校对:颜京宁)
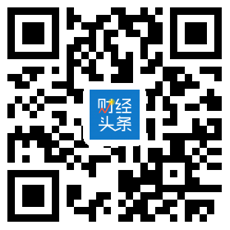
4000520066 欢迎批评指正
All Rights Reserved 新浪公司 版权所有