本文参考文献引用格式:刘鸿彦,李卫华,孙修圣.激光在钛制压力容器焊前清理上的应用[J].电焊机,2024,54(6):74-79. DOI:10.7512/j.issn.1001-2303.2024.06.12.
摘要
焊前清理是钛制压力容器制造过程中必不可少的关键步骤。采用激光清理技术对钛制压力容器的换热管与管板焊接接头进行了空间型结构的焊前清理试验,并对比了激光与常规打磨或丙酮清洗的传统焊前清理方式对焊接气孔产生及热影响区的影响。结果表明,激光清理方式对空间型结构的具有较高的可达性,对钛试板坡口的焊前清理效果优异,能够有效去除钛材表面的油脂、氧化物等污染物,显著降低焊接气孔的产生倾向,并可以抑制焊接接头热影响区“黑眼圈”的产生;焊后外观颜色与未处理区域相比,色差极小,几乎不影响焊缝外观;激光清理试样的抗拉强度分别为498MPa和515 MPa,均高于GB/T3621—2007标准规定的400MPa的最小抗拉强度要求。试验研究表明,激光清理工艺可以代替打磨、金属磨头刮擦、丙酮清洗等传统清理方式,为钛制压力容器的制造提供了一种高效、环保的新技术途径。
关键词
激光清理;纯钛TA2;焊前清理;压力容器
引言
随着我国石化能源行业的有序发展,钛、锆等有色金属及其复合板制压力容器的需求量逐步增多,为保证钛、锆等活性金属承压部件的焊接质量,需要对待焊区域进行有效的焊前清理,业内目前主要以机械清理和化学清洗两种方式进行,比如金属磨头、千叶轮、有机溶剂丙酮等,这些焊前清理工作在整个容器制造工艺过程中占据的工时损耗及人工成本相对较高,且清理一致性差,随着国家对环保方面重视程度逐步增加,酸洗式的化学清理也将逐步被淘汰,探索新的焊前清理技术成为研究的热点。
激光清理作为一种新型、清洁的材料表面清理技术,近年来在航空工业、轨道车辆及船舶行业等领域已逐步展开了相关研究并取得了较好的应用效果[1-6]。激光清理是利用高能激光束对材料表面进行处理,能够有效去除表面的氧化物、锈蚀和污染物,具有非接触、无磨损、可控性强等特点。文献[7]开展了对工业纯钛焊接接头氧化进行激光清理去除的研究,但就激光在压力容器焊前清理方面,目前鲜有研究或应用报道。基于此,在有色金属压力容器制造过程中开展激光清理这种新型的表面处理技术应用研究,对压力容器制造业的新技术探究及工艺流程改进有积极重要的意义。
本文为探索激光清理技术在钛制压力容器焊前清理中的应用,特别是针对换热管与管板焊接接头的空间型结构,通过对激光清理与传统清理方法的对比分析,评估其在提高清理效率、减少焊接缺陷和提升焊接接头性能方面的潜力。
试验材料、设备及工艺
01试验材料
本文主要针对压力容器钛材承压部件的焊前清理进行研究,试验用板材为工业纯钛,牌号TA2,化学成分如表1所示[8]。
表1 工业纯钛TA2化学成分(质量分数,%)
02试验设备
试验设备为国内某公司100 W便携式激光清理设备,该装置由轮式可移动端和便携式手持端组成,可以实现对工业纯钛TA2进行无损型表面微处理,如表面的油、污、粉尘类脏物;也可以进行多次反复的损伤型表面重处理,如表面的氧化渣、浮锈等污染。试验装置如图1所示。
03激光清理工艺
通过对TA2材料的激光表面清理装置的调试及试板试验,确定工业纯钛TA2的焊前激光表面清理工艺参数,具体如表2所示。
试验内容与结果分析
01换热管与管板坡口空间型结构清理试验
换热管与管板接头是换热类压力容器的关键结构,钛、锆等活性金属换热管与管板接头在焊接前都需要对坡口内侧、管板端面及管壁进行仔细有效的焊前清理工作。目前压力容器厂内的工艺流程主要采用清洗、抛磨、丙酮刷擦的方式进行,清理工作较繁琐,主要依靠人工完成,所以为考察激光在换热管与管板接头清理上的适用性,制作换热管与管板接头Mock-Up试件进行试验,如图2所示。
图2 清理前管头Mock-Up试件
将换热管穿入管板孔并组对好,为模拟换热器设备管头焊前清理的放置状态,将Mock-Up试件置于5FG位置[9]用激光器直接对换热管与管板接头端部的空间型结构进行焊前清理,清理过程如图3a所示。因穿管组对后换热管端面及管板坡口区域不在同一平面,属于空间型清理结构,清理难度相对较大,清理完成的试件状态如图3b、3c所示。
图3 管头焊前激光清理
对比清理前后试样可知,激光线可以将管板端面的油脂脏污快速地清理干净,并可以直接清理到狭小的坡口内侧及管端侧面。图3c中,能更明显地看出管子外壁清理到与未清理到的对比情况,未清理到的区域在管板孔内侧,属于不焊接区,对换热管与管板接头的焊接无影响;清理到的区域换热管外壁干净,清洁,呈现银白色纯钛光泽,属于焊接区,能够达到钛制换热管与管板接头焊前清理的要求。对清理后的接头端部进行GTAW焊接,焊接工艺参数见表3。焊丝符合ASME BPVC.Ⅱ.C篇中的SFA 5.16要求,成分与母材相匹配,焊接过程采用99.99%Ar进行焊枪保护及尾部保护。
表3 换热管与管板焊接工艺参数
为保证坡口根部完全熔透,采用点固和打底不填丝的方式进行焊接,电弧将管板及换热管母材自熔形成根部焊缝,盖面采用填丝焊方式进行,保证焊缝饱满。焊接完成的Mock-Up试件如图4所示。经过激光焊前清理的管头焊接外观效果优异,从焊后管板端面状态可以看出,管头焊缝银白色发亮,外观质量好,热影响区颜色同样呈现银白色,达到常规采用刷擦清理和丙酮清理的焊后表面状态,完全满足钛材换热器管头的施焊外观要求。为观察坡口根部的熔透情况,根据ASME BPVC.Ⅸ中QW193对换热管与管板试件测试要求,将管头焊缝焊缝“十”字切开,检测发现坡口根部完全熔透,满足标准规范及使用要求。由此可见激光焊前清理可以适用于压力容器换热管与管板焊接接头的工序过程,相比于传统刷擦清理和丙酮清理的人工方式,激光焊前清理一致性好,效率高,无须将换热管反复穿插清洗。部分管孔焊缝根部熔透情况如图5所示。
图4 焊后外观
图5 坡口根部熔透
02焊接气孔敏感性试验
钛制压力容器制造过程中,涉及到大量的钛材对接焊缝和角焊缝,而活性金属钛在焊接过程中,对气孔的敏感性很大,焊前清理的方式及效果直接影响焊接过程中的气孔倾向。在钛板焊接的工程实践中,焊前清理多为手工方式,在只采取打磨抛光,不采用金属磨头刮擦时,在焊接过程中会产生较多的焊接气孔,影响焊接质量,致使产品X射线检测不合格率增加,而金属磨头刮擦清理工作量大且繁琐,故考察激光在钛材板对接焊前清理上应用的可行性,并进行不同清理方式对焊接气孔影响的对比试验,如图6所示。
图6 坡口清理方式
选取同一块工业纯钛TA2试板,对试板划线分区,试板左侧仅采用激光的方式进行坡口清理,试板右端采用砂轮打磨后丙酮擦洗的方式进行坡口清理,对清理后的试板进行GTAW焊接,焊接工艺参数见表4。焊丝符合ASME BPVC.Ⅱ.C篇中的SFA 5.16要求,成分与母材相匹配,焊接过程采用99.99%Ar进行焊枪保护、尾部保护及背面保护。
表4 焊接工艺参数
焊接完成后对试板进行100%X射线检测,检测结果如图7所示。根据X射线检测结果,右侧区域未采用激光清理的试板在焊接完成后焊缝中存在三处连续密集型气孔见图7b,与工程实际焊接过程中常出现的气孔性质相符;左侧区域采用激光清理的试板在焊接完成后焊缝中只存在两处单点状微气孔见图7a,按照NB/T47013.2判定为Ⅱ级合格焊缝。结果说明激光在焊接坡口表面焊前清理上的运用,对减少砂轮打磨或金属磨头刮擦以消除焊接气孔倾向具有较好的作用。
图7 RT检测结果
对激光焊前清理的试板左侧区域取样进行抗拉强度及弯曲塑性检测,检测后试样如图8、图9所示。两件拉伸试样塑性断裂于母材区,抗拉强度分别为498 MPa和515 MPa,GB/T3621—2007《钛及钛合金板材》中对退火态TA2室温力学性能最小抗拉强度要求为400 MPa,拉伸试样检测结果高于母材标准规定的强度下限值,焊接接头拉伸试验合格;两件弯曲试样按照D=8t弯心直径的压头进行检测,弯曲后试样表面未产生开口缺陷,接头具备较好的塑性。结合无损检测和力学性能检测结果,验证了采用激光代替常规打磨、刷擦进行试板的焊前清理,能获得性能优异并符合标准要求的焊接接头。
03热影响区焊接氧化抑制试验
钛制压力容器制造过程中,对防止出现焊接氧化现象控制严格。根据制造规范及技术标准要求,需对钛焊缝和热影响区在焊接完工后的原始状态表面颜色进行检查[9],当焊缝和热影响区颜色为银白时为最理想状态,当呈现蓝、紫、灰等颜色时表明焊前清理效果不好或焊接惰性气体保护未执行到位,焊接接头可判定为不合格,不得用于承压焊缝。在工程实际中,当钛材焊接前的坡口清理按照酸洗或打磨方式处理时,即便焊接过程惰性气体保护得当,焊接完成后仍然会在焊缝两侧热影响区外产生深浅不一沿焊道方向的暗灰色印痕,工厂内通常俗称其为“黑眼圈”,影响焊缝的美观,原因主要是由于板材坡口两侧未完全清理干净,在焊接电弧的高温烘烤下产生颜色变化。为考察激光清理对该问题的表现,在焊接试验过程中同时观察清理方式对热影响区焊接氧化的情况。
试板左侧为激光清理的坡口,试板右侧为砂轮打磨+丙酮擦洗清理的坡口,焊接完成的打底焊试板如图10所示。对试板外观目视检查发现,试板右侧区域采用打磨+丙酮擦洗的坡口清理方式焊缝两侧受热影响产生的“黑眼圈”明显;经过激光焊前清理的试板左侧区域,打底完成后焊缝两侧受热影响产生的“黑眼圈”明显少于试板右侧区域,且痕迹很淡,基本未对焊缝外观产生不良影响,表明焊前坡口的激光清理方式对焊后“黑眼圈”的产生具有较好的抑制作用,可以在钛制压力容器承压部件制造过程中代替常规打磨配合丙酮清理的焊前坡口清理方式,并取得较好清理效果。
图10 不同清理方式焊后状态对比
结论
(1)验证了激光清理技术在钛制压力容器焊前清理中的高效性和适用性。激光清理对于换热管与管板焊接接头的空间型结构具有高可达性,能够实现对复杂结构的有效清理。
(2)激光清理显著降低了焊接过程中气孔的产生倾向。通过对比试验,激光清理的试板在焊接后仅发现极少数微气孔,而传统方法(打磨或丙酮清洗)处理的试板则出现了较多密集型气孔。
(3)激光清理有效抑制了焊接接头热影响区“黑眼圈”现象的产生,焊后外观颜色与未处理区域相比色差极小,提升了焊缝的整体美观度。
(4)激光清理后的焊接接头在力学性能测试中显示出优异的性能,抗拉强度高于GB/T3621—2007标准规定要求。
(5)激光清理作为一种非接触式清洁方法,避免了传统打磨和化学清洗可能带来的环境污染和健康风险,同时显著提高了清理效率。
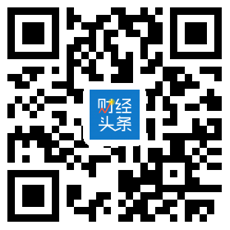
4000520066 欢迎批评指正
All Rights Reserved 新浪公司 版权所有