来源:半导体行业观察
1970 年,比尔·哈丁 (Bill Harding)设想了一条全自动晶圆生产线,该生产线可在不到一天的时间内生产出集成电路。这一目标不仅在 54 年前是大胆的,即使在今天价值数十亿美元的晶圆厂中也堪称大胆,因为先进集成电路的制造时间以周而不是天来计算。当时,诸如随机存取存储器芯片之类的集成电路通常需要经过数十个手动工作站,在一个月内走走停停地生产出来。
当时,哈丁是位于纽约州东菲什基尔的 IBM 制造研究小组的经理。他将领导一个如今几乎无人知晓的、旨在实现其愿景的项目,该项目被称为 SWIFT 项目。要实现如此惊人的短周转时间,需要一定的自动化水平,而这只有通过集成电路生产线设计的范式转变才能实现。哈丁和他的团队做到了这一点,他们取得的进步最终将反映在全球半导体行业。SWIFT 的许多突破性创新如今在高度自动化的芯片制造厂中已司空见惯,但 SWIFT 令人难以置信的短周转时间从未被超越。
SWIFT 平均需要 5 小时才能完成其制造工艺的每一层,而最快的现代晶圆厂每处理一层需要 19 小时,行业平均时间为 36 小时。尽管当今的集成电路采用更多层构建,晶圆尺寸更大(小比萨饼大小),而且处理过程也更复杂,但这些因素并不能完全弥补差距。哈丁的自动化生产线确实非常快。
半导体制造宣言
我(指代本文作者,下同Jesse Aronstein)第一次遇到哈丁是在 1962 年,当时我本以为这是最后一次。当时 IBM正准备生产其首台全固态计算机System/360。这次会面有些坎坷。当我演示如何自动批量处理未封装的微型半导体芯片进行测试和分类时,他对我吼道:“这到底有什么用?”
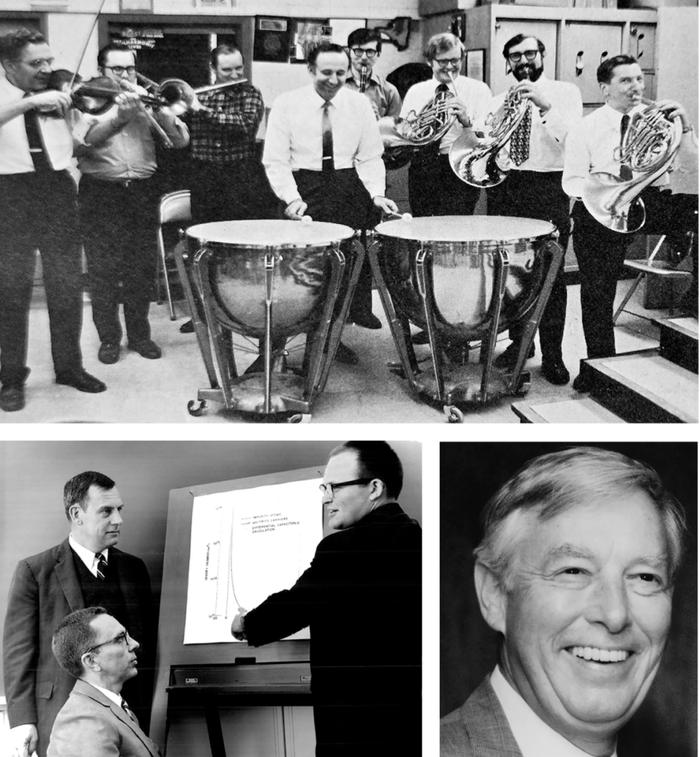
威廉·E·(“比尔”)·哈丁是一位创新思想家和发明家。1961年, IBM 新成立的零部件部门成立时,他已经在 IBM 工作了三年,从事半导体及其制造技术开发。哈丁成为新部门的中层经理,负责开发和生产制造 System/360 固态设备和电路模块所需的设备。
作为 IBM 经理,他有点粗鲁。但对于一个在纽约布鲁克林长大、在乔治·S·巴顿将军的第三军服役期间在二战中三次受伤的人来说,这也许是意料之中的事。战后,哈丁获得了数学和物理学学士和硕士学位,并成为 IEEE 会员。
1961 年,我加入 IBM,之前在通用电气从事火箭发动机开发工作。和当时的大多数工程师一样,我对半导体制造一无所知。五年前,我参加了一门真空管电子学课程,教授将晶体管描述为“一种实验室奇观,可能永远不会有任何成就。”

SWIFT 项目占据了 IBM 庞大的东菲什基尔半导体工厂 310 号楼的一小块空间(图中黄色部分)
每次我和哈丁相遇,他粗鲁无礼的举止都会浮现出来。如果他曾经上过 IBM “魅力学校”(管理培训),那也看不出有什么明显的证据。尽管如此,他还是成功完成了任务。到 1964 年,System/360 的固态逻辑模块从位于东菲什基尔一个前农场的零部件部门新工厂流出。
1970 年 7 月,在完成三年的研究生学习后,我回到了 IBM。在学习中断之前,我担任了四年的一级经理,不想再从事管理工作。我想要一份纯粹的技术职业,于是我加入了 East Fishkill 的制造研究 (MR) 小组,希望能得到这样的工作。
后来我和哈丁又有了交集。1970 年 8 月中旬,他成为 MR 的高管。在此之前,他花了一年时间制定 IBM 公司未来制造和使用 超大规模集成电路(VLSI) 的企业战略。他被任命为 MR 的负责人,以证明其制造理念的可行性。
MR 召开了一次员工大会,宣布了管理层变动。在介绍之后,哈丁描述了他对未来 VLSI 应用和制造的看法。以下是他的主要观点:
VLSI 电路将基于场效应晶体管技术(当时双极结型晶体管占主导地位);
无缺陷的高产量至关重要;
制造业将完全自动化;
每次处理一块晶圆可获得最佳效果;
较短的周转时间将带来重要的好处;
通过复制成功的生产线,产量将会扩大。
教育讲座结束后,哈丁从教授变成了指挥官,就像巴顿将军一样。MR 的唯一使命是展示哈丁的想法,与该目标不符的正在进行的项目将被转移到 IBM 的其他地方或被放弃。MR 将证明可以构建一个自动化系统,每天处理大约 100 个晶圆,一次一个,产量高,周转时间为一天。
什么?我没听错吧?从裸晶圆到成品电路,一天的周转时间就是我们现在所说的“登月计划”。记住,当时通常需要一个多月的时间。他是认真的吗?
哈丁知道这在理论上是可行的,他决心实现它。他宣称,如果原型实验 IC 设计能够在一天内而不是几个月内生产出来,IBM 将拥有巨大的竞争优势。他希望电路设计师在将数字描述提交给生产线后的第二天就能拥有可测试的电路。
哈丁立即在 MR 内部组织了一个设备组和一个工艺组,并任命我负责管理设备组。我不想再当经理了。现在,我勉强成为了二级经理,负责为一条尚未确定的生产线开发所有的加工和晶圆处理设备,而我当时几乎还没有开始设想这条生产线。我梦想中的研究工作只持续了一个多月。
Walter J. (“Wally”) Kleinfelder调入 MR 负责管理工艺组。他们会选择要制造的产品并定义制造工艺——获取空白硅片并在其表面高产地构建集成电路所需的化学、热和光刻步骤的详细顺序。
克莱因费尔德选择了随机存取存储器芯片 IBM RAM II 进行演示。该产品在东菲什基尔现场生产,因此我们拥有制造该产品所需的一切,并根据现有的非自动化生产线评估我们的结果。
IBM 的 SWIFT 试点晶圆厂拥有一辆单轨“出租车”
集成电路制造首先需要在硅片表面的适当位置制作晶体管和其他元件,然后通过添加一层经过选择性蚀刻的铝薄膜来创建所需的布线图案,从而将它们连接在一起。这种导体薄膜被称为布线层或金属化层。
IC 制造使用光刻技术来创建制造 IC 所需的多个层,每个层都有独特的图案。这些层包括金属布线层,如今,一个先进的芯片可能有十几个金属布线层。在这些步骤中,晶圆上的金属层涂有感光光刻胶材料,然后将图案的图像曝光在其上。将要形成导体的区域挡住光线。图像显影后,从曝光的图案区域去除光刻胶,使这些区域能够被酸蚀刻。其余表面仍受到耐酸光刻胶的保护。蚀刻完成后,去除剩余的保护光刻胶,只留下所需图案的布线层。
SWIFT 项目概览
Project SWIFT 生产线基于五个“区域”。每个区域都是一个封闭的汽车大小的机器,在光刻掩模图案曝光之间执行所有工艺步骤。除了第一和第五个区域外,晶圆进入一个区域时,光刻胶已曝光,准备显影;离开该区域时,光刻胶已新鲜,准备进行下一次图案曝光。出租车将单个晶圆从一个区域运送到光刻图案曝光站,然后按顺序运送到下一个区域。
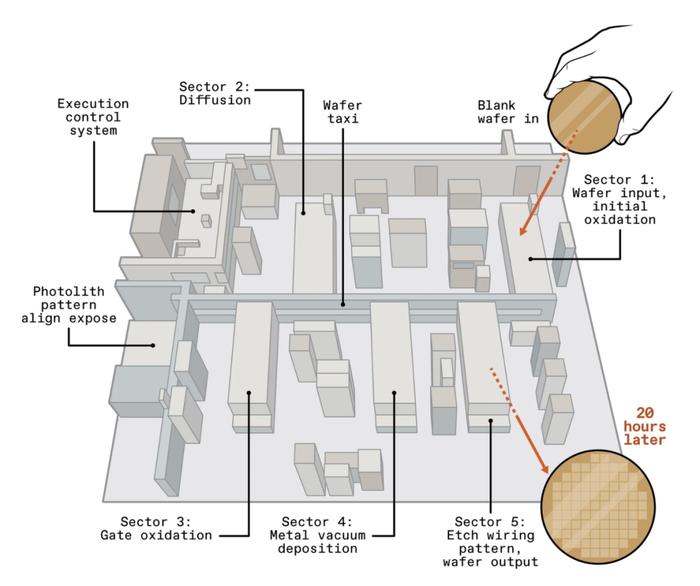
WIFT 生产线由三级控制系统控制。最高层由一台 IBM 1800 计算机负责总体管理。它与五个加工区的每个控制器进行通信,加工区内有加工和晶圆处理子区,其中一些子区有自己的控制器。
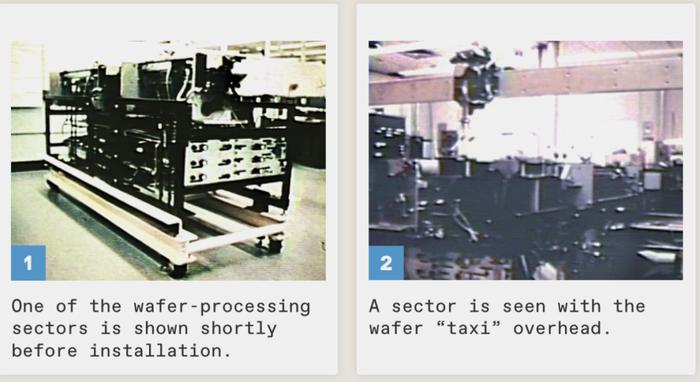
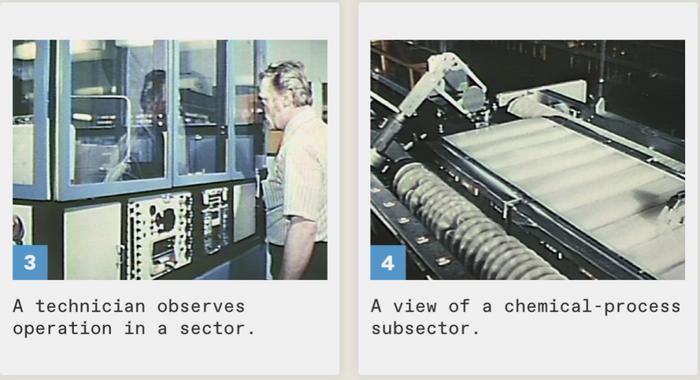

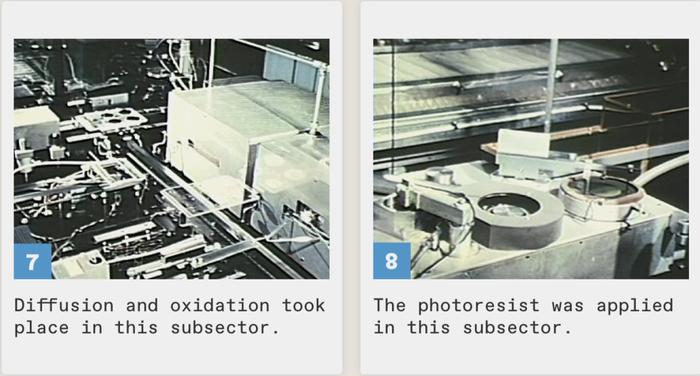

IC 工艺还使用光刻技术在硅片上制造晶体管和其他元件。在此,绝缘层上蚀刻出开口,通过这些开口可以将微量的特定杂质注入纯硅的暴露点中,以改变电气特性。生产 RAM-II IC 需要使用四种不同的图案进行四次单独的光刻操作:三种用于制造晶体管和其他元件,一种用于制造金属布线层。这四种图案必须完全对齐才能成功制造芯片。
光刻然而,这只是 IC 制造过程的一部分。在现有的生产线上,处理 RAM-II 晶圆需要数周时间。但原始处理时间(晶圆在各种热、光刻、化学和沉积站实际处理的时间)不到 48 小时。晶圆的大部分时间都花在等待下一个工艺步骤上。如果晶圆从一个步骤快速进展到下一个步骤,则可以省去某些步骤,尤其是化学清洗。
克莱因菲尔德的团队负责确定哪些步骤可以省略,哪些步骤可以加速。最终的原始工艺时间不到 15 小时。然后, 我的化学设备开发经理Maung Htoo负责测试提议的工艺。他的团队将直径 1.25 英寸的晶圆放入“锅碗瓢盆”实验室设备中,对其进行评估和改进。正如预期的那样,简化的程序在大约 15 小时内成功生产出工作电路。
自动化系统架构得以实现。最初设想是一系列相连的机器,每台机器执行流程的一步,就像汽车装配线一样。但必须考虑到设备停机时间,以进行预防性维护和故障维修。这是通过插入短期存储“缓冲区”来实现的,这些缓冲区可在必要时将晶圆暂时存储在工艺链中的选定点。
这一工艺链概念因与光刻图案成像 相关的考虑而进一步被颠覆。当时,光刻胶在晶圆上的曝光通常通过类似于照相接触印刷的工艺完成。光刻掩模相当于照相底片,当曝光光刻胶时,光线会穿过光刻掩模。掩模上的任何缺陷或颗粒都会导致芯片上出现相应的缺陷,在同一个位置,一片又一片晶圆。
东菲什基尔光刻小组开发了一种非接触式 10:1 缩小 步进重复图像投影仪。可以将其视为一种摄影幻灯片投影仪,可产生缩小的图像,其中包含芯片上单个层的图案。然后,它“步进”穿过晶圆,一次曝光一个芯片位置。相对于接触式掩模,步进式光刻机对颗粒污染的敏感度更低,因为任何杂散颗粒的阴影尺寸都会缩小 10:1。其他优势包括更高的光学分辨率和更长的掩模寿命。
但是,由于速度较慢,因此需要多台步进机才能达到产量目标。为了在每个晶圆上实现最佳图案对准以实现多次图案曝光,需要将晶圆送回同一台步进机,以对工艺链中的每一层进行曝光。这样可以消除因机器之间的细微差异而引起的图像失真的影响。然后,构建 RAM-II 电路需要晶圆四次单独前往其指定的步进机。这将线性序列分为五个区段。单轨“出租车”会将晶圆从一个处理区段运送到其指定的步进机,然后再返回将其运送到下一个区段。
设想将五个区域中的每一个区域都设计成一个封闭空间,其中包含完成该工艺链部分所需的所有自动晶圆加工和处理设备。区域封闭空间和滑行舱的设计将为晶圆提供洁净室质量的局部环境。在区域封闭空间内,晶圆通常会直接从湿化学模块传送到微型熔炉,再传送到光刻胶应用模块,最后传送到滑行舱的取件口。例如,在湿化学模块内,晶圆将接受清洁、光刻胶显影和去除、蚀刻等程序。
整条生产线的控制将分三个层次完成。整个生产线管理、记录保存、滑行物流和过程监控将由中央计算机系统处理。每个区域均有专用控制器,负责管理区域内的晶圆物流,并将晶圆流量和处理数据反馈给中央系统。每个区域外壳内的各个处理和晶圆处理模块将根据需要拥有自己的专用控制器,以进行独立设置和维护。
最终配置完成后,我们的 RAM-II 芯片自动化演示线将由五个部门、一辆出租车和一个光刻图案成像中心组成,全部由计算机管理。哈丁接任六个月后,MR 开始设计和建造实际系统。
傲慢的中层经理从文学中寻找灵感
哈丁经常前往位于纽约州阿蒙克的 IBM 总部,汇报进展、请求资源、反驳挑战,并说服高层领导,这笔钱是对未来的良好投资。这是一项艰巨的任务。他每周召开的冗长的员工会议常常反映出他所承受的压力。他会就他知道我们知道的事情发表长篇大论,讲寓言故事,并进行类比。
当时,我并没有意识到他正在利用员工会议来制定和完善阿蒙克演示的想法。他注意到了我们的反应,并相应地调整了他的演示想法。他向高层领导的演示非常有效。在项目持续约三年的时间里,MR 获得了开发、设计、构建和运营整个系统所需的所有资金和支持。
在一次员工会议上,哈丁大声朗读了海伍德·布朗的短篇小说《The 51st Dragon》,以强调名称或口号激励人们实现不可能的力量。当然,他的观点是,我们需要为这个项目起一个非常好的名字。最终选择了“SWIFT”。哈丁一直坚持认为这不是一个缩写词,但人们仍然认为它是“半导体晶圆集成工厂技术”(Semiconductor Wafer Integrated Factory Technology)的简写。
SWIFT 的加工和晶圆处理设备完全由 IBM 的零部件部门定制设计。主要设计目标是自动、一致、均匀地处理晶圆,并保持晶圆清洁无损。晶圆处理实验选出了最清洁、最温和的技术。处理设备的设计目的是支撑晶圆,而不是抓住晶圆。一种新颖的晶圆处理器利用晶圆上方的气流将其抬起,而无需物理接触,成功地应用于一些晶圆传输动作。
SWIFT 处理设备的“清洁而温和”设计有一个例外。位于佛蒙特州伯灵顿的零部件部门管理层向 Harding 施压,要求其使用他们开发的“气轨”晶圆运输设备。该设备利用气流来提升和移动晶圆,就像空气曲棍球比赛中的冰球一样。Harding 需要伯灵顿的持续支持,因此他下令在 SWIFT 中使用一些气轨设备。尽管晶圆污染和可靠性问题尚未解决,但 Harding 还是这样做了。
另一项自上而下的命令解释了为什么 SWIFT 最终采用两种不同类型的部门控制系统 - 这与良好的可维护性设计背道而驰。我们设计了一个定制控制器,并建造了五个单元(每个部门一个),这时总部要求我们采用新发布的 IBM System/7,它是专门为工厂设备和过程控制应用开发的。毕竟,如果 IBM 本身不在自己的先进生产线上使用计算机,潜在客户会想“为什么不呢?”但如果 SWIFT 使用 System/7,并且该项目被证明是成功的,它将有助于销售 System/7。因此,对于这五个部门,SWIFT 最终采用了四个定制控制器和一个 System/7。两种类型都运行良好。
设备可靠性是 SWIFT 的致命弱点。为了实现高可靠性和易于维护,某些机制和控件被标准化以供整个系统使用,并且选择它们是因为可靠性和简单性,而不是新颖性或优雅性。例如,观察系统运行的人会注意到许多动作是以离散的平滑步骤而不是单一的横向移动完成的。这一特性的背后是简单、坚固且可靠的 日内瓦驱动器的广泛使用,它最初是几个世纪前为钟表开发的,但现在适用于必须平滑且在端点精确锁定的线性和旋转运动。日内瓦驱动器的输入轴每轻松控制转动一次,就走一步。长横向移动需要轴转动多次,从而导致奇怪的运动。
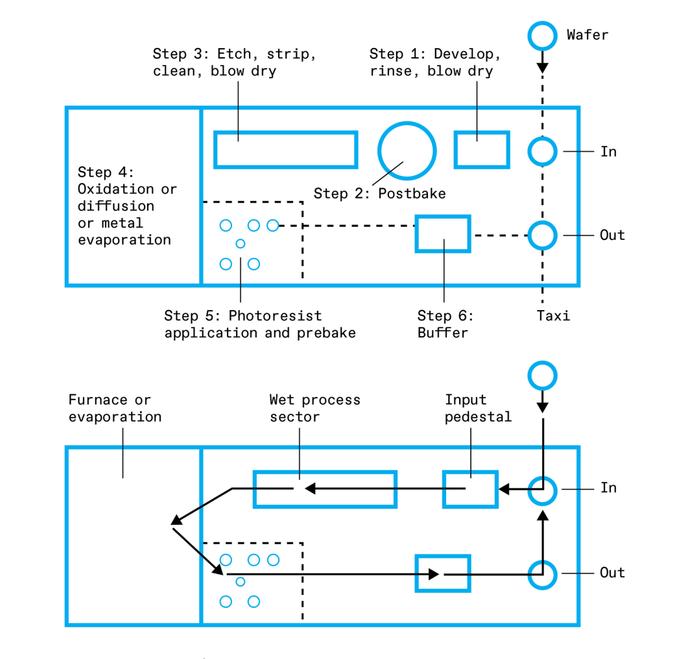
另一项简化涉及旋转晶圆,以离心方式散布液态光刻胶,然后滴在晶圆中心。在现有生产线中,“错误的旋转速度”经常被认为是光刻胶相关晶圆加工不合格的原因。通过用同步交流电机驱动 SWIFT 的旋转器,旋转速度不再是变量,这些电机由 60 赫兹交流电源锁定为 3,600 rpm,就像驱动留声机转盘一样。无需速度控制器。通过调整其余变量(温度、粘度和/或旋转时间),可实现所需的光刻胶膜厚度。最后,通过消除四个单独的速度控制器,系统可靠性得到了提高。
随着 SWIFT 从空想概念发展到实际硬件实施,Harding 调整了 MR 的组织结构,并获得了支持团队的合作。他确保他的员工拥有完成工作的资源,并可以专注于项目。我开始钦佩他的组织能力以及从公司内部挑选和招募顶尖人才的能力。
哈丁成立了一个小组来开发 SWIFT 的主控制系统,该系统监控每个晶圆在各个区域移动时的进度。该执行控制系统 (ECS) 基于 IBM 1800。每个晶圆都有一个序列号,并在生产线的每一步都进行跟踪。ECS 存储和监控每个晶圆的加工参数,检测并快速应对不合格情况。它的打孔卡和磁带盒以今天的标准来看似乎有些过时,但它是晶圆生产线生产控制和监控方面的一项重大进步。
他还把由 Sam Campbell 管理的整个仪表部门从 IBM Endicott 转移到了 East Fishkill。Campbell 的部门随后为 SWIFT 开发了开创性的实时现场过程控制方法。
半导体制造业短暂的一生却留下了持久的遗产
建造并测试了熔炉和化学处理器的模型。东菲什基尔制造工程集团的Robert J. Straub部门设计并建造了这些部门以及其中的加工设备模块。哈丁请来Bevan PF Wu管理生产线的安装、调试和运行。随着设备和设施在 SWIFT 专用的 4,000 平方英尺空间中合并,Rolf H. Brunner负责吴的安装、启动和调试,他曾管理过大部分部门设计以及真空金属沉积设备的开发工作。
整个过程中只有一个操作没有完全自动化。晶圆对准以将图案曝光在光刻胶上仍然需要训练有素的操作员。SWIFT 的最终版本既有 10:1 光学步进机,也有 1:1 接触式掩模机,但事实上,大多数芯片都是用 1:1 机器生产的,因为这样产量更高。
到 1973 年底,IBM 总部已经确信晶圆加工的全自动化可以成功。因此,这一目标被作为新晶圆加工线的主要目标,用于生产 IBM 下一代计算机“FS”(未来系统 )的电路。拟建的新生产线被称为“FMS”(未来制造系统),SWIFT 更名为“FMS 可行性生产线”。
Bevan Wu 成功地管理了生产线的完工、试运行、人员培训以及设备、工艺和程序的改进。他使生产线达到生产 IBM 产品电路的水平。该系统在 1974 年中期至 1975 年初进行了五次连续运行。在运行期间,他的团队分析了结果并实施了改进。最长的连续运行持续了 12 天。晶圆产量平均为每天 58 片晶圆,是其设计最大值的 83%。从裸晶圆输入到可测试电路输出的平均周转时间约为 20 小时。原始处理时间为 14 小时。最终产量与 East Fishkill 的传统 RAM-II 生产线有史以来的最佳产量持平。
IBM 全球各地共有 135 名技术人员、工程师和管理人员接受了系统操作培训,生产出 600 个产品级晶圆,其中包含 17,000 个 RAM-II FET 内存芯片。
但就像他的二战指挥官巴顿将军一样,哈丁被绕过去领导“大戏”——对哈丁来说,就是创造新的 FMS 自动化生产线。他放弃了管理职业阶梯,被提拔为 IBM 院士,这是公司中最高的非管理级别。
FMS 可行性生产线(最初称为 SWIFT)于 1975 年初进行了最后一次连续运行。它已经完成了目标。现在需要它的人员帮助创建 FMS 生产线以生产 FS 计算机。但在 1975 年晚些时候,FS 项目被取消,FMS 变得多余。一部分运往 FMS 的设备成为了 East Fishkill 的 QTAT(快速周转时间)生产线,这是 IBM 的一项开创性成果,比其鲜为人知的前身 SWIFT 项目更令人难忘。
尽管 SWIFT 的寿命很短,而且从未成为众人关注的焦点,但它的众多创新在当今的半导体工厂中清晰可见。与 SWIFT 一样,这些工厂高度自动化且由计算机控制;拥有中央传输系统和“伯努利”处理器,利用气流提升晶圆而无需物理接触;在氧化物或金属膜形成后立即涂上抗蚀剂;使用步进机进行光刻图案曝光;并采用实时过程控制。所有这些都是 50 年前 SWIFT 项目的突破性特点。
在 Harding 手下为 SWIFT 工作三年的经历对我来说是一次蜕变。一开始的惶恐最终化为钦佩。我开始认为 Bill Harding 是一位真正的天才,他有自己的独特之处。在他独特的管理风格的激励和支持下,一小群敬业的人取得了远超任何人最初设想的成就。甚至超出了我们自己的想象。
我们认为行业中的第一批成就者是其发明的现代体现的“父亲”。人们通常这样称呼爱迪生、贝尔、福特和莱特兄弟。从这个意义上讲,威廉·E·哈丁显然是现代、自动化、价值数十亿美元的工厂之父。
参考链接
https://spectrum.ieee.org/semiconductor-fabrication
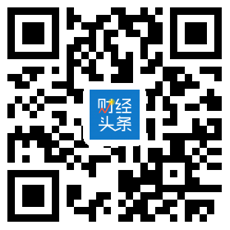
4000520066 欢迎批评指正
All Rights Reserved 新浪公司 版权所有