在当今竞争激烈的制造业环境中,企业要想保持领先地位,就必须不断优化生产流程,提升生产效率,并增强生产的灵活性。优化精益布局作为一种先进的生产管理理念,正成为众多企业转型升级的关键。本文将从精益布局的基本概念出发,探讨如何通过优化精益布局来实现生产效率的提升和灵活性的增强,同时分析实施过程中可能遇到的挑战及应对策略。
一、精益布局概述精益布局,又称精益生产布局或精益工厂设计,是一种以减少浪费、提高效率和灵活性为目标的生产系统设计方法。它强调在现有资源条件下,通过重新配置生产设备、优化工作流程、减少物料搬运距离和时间等手段,达到生产效率最大化、生产成本最小化的目的。精益布局的核心在于“流动”和“拉动”两大原则,即确保生产流程顺畅无阻,按需生产,避免库存积压。二、优化精益布局的策略与实践2.1 价值流分析价值流分析是精益布局的第一步,它要求企业从原材料采购到产品交付给客户的全过程进行审视,识别并消除其中的非增值活动。通过绘制价值流图,企业可以清晰地看到生产流程中的瓶颈环节和浪费点,为后续的优化工作提供方向。例如,某汽车制造企业通过价值流分析发现,其零部件从仓库到生产线的搬运过程耗时较长,且多次转运增加了损坏风险。针对这一问题,企业决定采用“超市式”物料配送系统,将零部件直接放置在生产线旁的物料架上,实现了即时取用,显著提高了生产效率。2.2 单元化生产单元化生产是精益布局的重要实践之一,它通过将生产设备、人员和工作任务按照产品族或工艺流程进行组合,形成一个个相对独立的生产单元。这种布局方式有利于减少物料搬运、缩短生产周期、提高生产灵活性。例如,一家电子产品制造商在实施单元化生产后,将原本分散在不同车间的组装、测试、包装等工序整合到同一个生产单元内,实现了从原材料到成品的一站式生产,大大提升了生产效率和产品质量。2.3 5S与可视化管理5S(整理、整顿、清扫、清洁、素养)是精益布局的基础,它通过对生产现场进行整理、整顿,保持工作环境的整洁有序,提高员工的工作效率和安全意识。同时,可视化管理作为5S的延伸,通过标识、颜色、图表等手段,将生产过程中的关键信息直观展现,便于员工快速识别问题、采取措施。例如,在一条自动化生产线上,企业通过在关键工位设置质量报警灯,一旦检测到产品缺陷,立即亮起红灯,提醒操作人员及时干预,有效降低了不良品率。2.4 持续改进与员工培训精益布局不是一次性的项目,而是一个持续优化的过程。企业需要建立持续改进的文化,鼓励员工提出改进建议,定期评估生产流程,寻找潜在的优化空间。同时,员工培训也是精益布局成功实施的关键。通过培训,员工可以掌握精益生产的理念和方法,提高解决问题的能力,为生产流程的优化提供智力支持。例如,某企业通过设立“精益改善小组”,鼓励员工跨部门合作,共同解决生产中的难题,同时定期举办精益生产培训班,提升全员精益素养。三、面临的挑战及应对策略尽管优化精益布局能够显著提升生产效率和灵活性,但在实施过程中,企业也会面临诸多挑战。3.1 初始投资与成本控制精益布局往往需要一定的初期投资,包括设备购置、生产线改造、员工培训等方面的费用。对于资金紧张的企业来说,这无疑是一大难题。应对策略是,企业可以分阶段实施精益布局,优先改造关键生产环节,逐步扩大成果;同时,通过提高生产效率、降低浪费来弥补初期投资成本。3.2 员工抵触与变革管理精益布局往往伴随着工作流程的调整和岗位职责的变化,这可能会引发员工的抵触情绪。应对策略是,企业应加强沟通,让员工理解精益布局的目的和意义,同时提供必要的培训和支持,帮助员工适应新的工作环境和角色。此外,通过建立激励机制,如设立精益改善奖励,激发员工的参与热情和创造力。3.3 持续改进与维持精益布局是一个持续改进的过程,需要企业建立长效机制,确保生产流程不断优化。然而,随着时间的推移,员工可能会产生懈怠情绪,导致精益成果难以维持。应对策略是,企业应将精益理念融入企业文化,形成全员参与、持续改进的良好氛围;同时,建立定期评估机制,对精益成果进行量化评估,确保持续改进的有效性。四、结语优化精益布局是提升企业生产效率、增强灵活性的有效途径。通过价值流分析、单元化生产、5S与可视化管理、持续改进与员工培训等措施,企业可以逐步构建起高效、灵活的生产体系。当然,在实施过程中,企业也会面临诸多挑战,但只要坚定信念、科学规划、精心组织,就一定能够克服困难,实现生产效率和灵活性的双重提升。未来,随着智能制造、大数据等先进技术的不断发展,精益布局将拥有更加广阔的应用前景,为企业创造更大的价值。
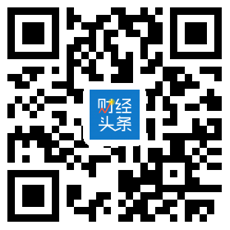
4000520066 欢迎批评指正
All Rights Reserved 新浪公司 版权所有