随着全球塑料制品市场的不断扩大和技术的不断革新,热成型机多腔模具的设计已成为塑料制品行业十分关注的话题。在塑料成型工艺中,模具的设计直接影响生产效率、产品质量、成本控制等,因此深入研究热成型多腔模具的设计原理和技术,对提高生产效率、降低成本至关重要。
1、热成型多腔模具的基本原理
热成型多腔模具是利用加热系统将塑料原料加热至熔融状态,再通过流道系统将熔融的塑料注入模腔进行成型的模具。与传统的单腔模具相比,多腔模具可以同时成型多个产品,生产效率更高,成本更低。
2.设计要点及技术考虑
材料选择及耐热性:模具材料的选择是影响模具性能的重要因素之一,常用的模具材料有工具钢、不锈钢等,需要根据具体的成型温度和塑料材料特性合理选择材料,以保证模具具有良好的耐热性和力学性能。
2.1流道设计:流道的设计直接影响塑料在模具内的流动,影响制品成型质量和生产效率。流道结构设计合理,塑料流动均匀,避免气泡、熔接线等缺陷。
2.2冷却系统:冷却系统的设计影响模具的冷却速度和均匀性,直接影响生产周期和产品质量。通过合理的冷却系统设计,可以提高模具冷却效率,缩短成型周期,降低生产成本。
2.3型腔设计:型腔设计需要根据产品的结构特点和成型工艺要求进行合理的设计,以保证模具能够精确复制产品的形状和尺寸,同时尽量减少产品成型过程中的应力和变形。
2.4温控系统:温控系统的稳定性对于塑料热成型机工艺至关重要。通过精确的温控系统,可以保证模具温度的稳定性,避免温度波动引起的质量问题。
2.5成型机构:成型机构的设计需要考虑模具的结构特点和成型工艺要求,以保证模具能够准确、稳定地开合,避免因开合不良而导致产品缺陷。
3.热成型多腔模具的优势与挑战
热成型多腔模具与传统的单腔模具相比具有生产效率高、成本低、产品质量稳定等诸多优势。但其设计和制造工艺也面临着挑战,例如流道设计复杂、冷却系统控制困难等。因此设计人员需要具备较高的专业水平和丰富的经验,才能设计出优质高效的热成型多腔模具。
4.热成型技术在模具设计中的应用
在热成型多腔模具设计中,自动化热成型技术起着重要作用。通过控制模具温度,可以有效解决塑料在成型过程中的收缩和变形问题,提高产品精度和表面质量。此外,合理的热流道设计可以实现塑料材料均匀填充,减少气泡、缺料等缺陷,改善产品外观和性能。
5.多腔布局与优化
多腔布局与优化是热成型多腔模具设计的关键方面。在布局设计中,需要考虑产品结构、尺寸、成型工艺等因素,确定腔数和位置,以达到最佳成型效果。在优化设计中,可以通过优化流道结构、增加冷却系统、改善排气系统等进一步提高模具性能和稳定性。
6. 材料选择与加工工艺
在热成型多腔模具设计中,材料选择与加工工艺同样重要。模具材料需要具有良好的耐热性、硬度、耐磨性,以保证长期稳定运行。同时,需要选择适当的加工工艺,如数控加工、电火花加工等。根据产品要求和生产规模,保证模具的精度和可靠性。
7.模具的维护与管理
最后,压塑机多腔模具的维护与管理是保证其长期稳定运行的关键。定期检查模具的磨损和损坏情况,及时修复和更换,以保证模具的完整和稳定的性能。同时,建立科学的模具管理制度,加强模具使用和维护方面的培训,可以提高模具的利用率和使用寿命。
总之,热成型多腔模具的设计涉及多个方面,需要综合考虑材料、工艺、布局等,才能达到最佳的成型效果和经济效益。只有不断探索创新,不断提高设计和技术水平,才能在激烈的市场竞争中立于不败之地。
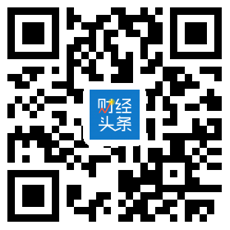
4000520066 欢迎批评指正
All Rights Reserved 新浪公司 版权所有