
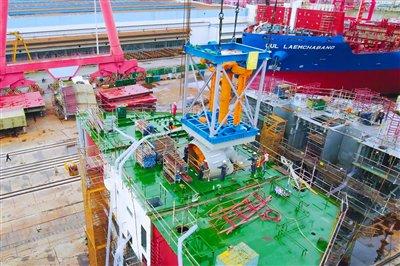


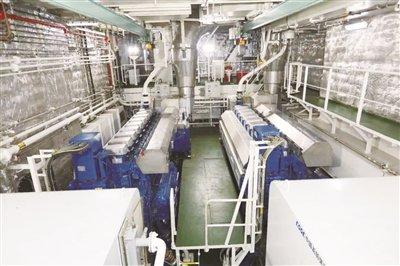
□ 通讯员 夏小健
1241台套设备、48696根管系、1200公里电缆……建造“梦想”号堪称是一个极为复杂的“巨系统”工程。然而,在面临国外技术垄断、供应链阻塞等状况时,如何高质量且按期交付,这对黄埔文冲的建造者而言是一项艰巨的考验。
近日,笔者到访黄埔文冲船厂,了解“梦想”号的建造过程以及其中的关键环节。
分场地分区域分阶段建造
为按期交船,在资源场地有限的情况下,黄埔文冲决定全厂动员,采用分场地、分区域、分阶段的建造方案。简单来说,就是将全船划分为艏部、舯部、艉部、上建四个区域,分别在水平船台、室内船台、船坞同步建造,最终通过搭积木的方式进行合拢。通过打破船舶建造的常规逻辑顺序,以空间换时间,以牺牲阶段完整性换时间,从而将设计、采购对生产的影响降到最低。
2022年11月20日,重达7000吨的“梦想”号艏部巨型总段通过移船小车和模块车转运到浮船坞,然后再从浮船坞转运到室内船台与艉半船对接,完成主船体大合拢,这是船厂首次应用该建造方法。
为此,船厂创造了一套基于数字孪生测控网的异地半船建造精度控制方法。在数字孪生测控网中,不同总段的建造处于同一坐标系,船体各个结构的定位基准误差控制在毫米级,保证合拢端面相互匹配。
打造船舶硬核“心脏”
要达成“梦想”号的多种功能,其强大的能源供应起着关键作用。“梦想”号运用新型蓄能闭环电网技术,电站容量高达30兆瓦。其电网由6台电压6600伏、功率5000千瓦的柴油发电机组、1100千瓦时三元锂电池组以及电池管理系统所构成。
“梦想”号全船电力系统分布于三个防火分隔区域。在闭环模式下,全船电力供应能够实现共享,仅需2台主发电机同时运行,便可满足作业需求,有效避免了能源的浪费。即便任何单个舱室出现严重故障,其他舱室也不会受到牵连,不会产生“一处短路、全船断电”的现象。
2024年10月5日,船厂在“梦想”号试航中进行了电网短路试验,验证电网自身保护动作的快速性、准确性以及系统的故障穿越能力。该实验风险极大,瞬间最大短路电流可达30000安,是普通家庭电线所能承载最大电流20安的1500倍。开始试验前,船厂事先准备短路试验方案和试验工装,并开展了模拟故障摸底,反复斟酌和严格把控每一个细节,最后一次性成功完成试验。
值得关注的是,该船电缆施工的工作量与难度均属空前。从电站起始,船上7台推进器以及各类用电设备凭借长达1200公里的电缆相互连接,其长度是相同尺度集装箱/散货船的十多倍。“艏部是全船电缆铺设最为密集之处,最多采用了11层电缆托架。由于部分设备到货延迟,电缆铺设无法一次性完成。在电缆托架本就狭小的状况下,还得为后续电缆铺设预留空间。在最为繁忙之时,一线员工单人承担的工作量约是普通船只的三四倍。”负责该项工作的智增辉说。
实现海中“不动如山”
“梦想”号的设计要求是在6级海况下能够正常作业,长达数千米乃至万米的钻杆必须如“定海神针”般稳稳地钻入海床之中,那么“梦想”号究竟是怎样做到的呢?
答案就在“梦想”号的动力系统里。它配备了3台4000千瓦全回转主推、3台3500千瓦全回转伸缩推以及1台1500千瓦侧推,动力定位能力达到国际最高的DP-3级。在波涛汹涌之中,它能够借助卫星定位、声呐定位、罗经、运动参考系统(MRU)等传感器计算外界环境力,进而自动向推进器发出逆向推进指令,达成在海中“不动如山”的效果。
其中,3台全回转伸缩推是船厂迄今为止所总装完成的最大伸缩推,首次采用焊接密封工艺,并且首次运用3D全站仪进行精度控制。为了顺利完成试验,船厂把带有伸缩推的总段在5米高的支撑上进行搭载,不带伸缩推的总段则在传统坞墩上搭载。在试验结束之后,再将处于高处的总段起吊下降至传统坞墩的高度以便进行合拢。
不过,成功安装仅仅是开端,调试试验更是严峻的挑战。由于每个推进器都涉及多个厂家,前期技术协议不够明确,导致设备与系统之间的通讯接口存在诸多问题,在调试过程中需要多次修改,其工作量是具备DP-2功能船舶的5倍以上。“梦想”号于2023年9月22日启动主推调试工作,船厂专门成立主动力调试小组,做到设计问题不过夜、追溯必有反馈。历经两个月的时间,调试小组成功完成了全船主动力系统的调试工作。
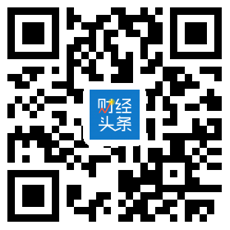
4000520066 欢迎批评指正
All Rights Reserved 新浪公司 版权所有