(报告出品方:中信证券)
数控机床产业链:工业母机,自主可控的核心
数控机床零部件主要包括铸件、钣焊(金)件、精密件、功能部件、数控系统及电器 元件构成。铸件是用各种铸造方法获得的金属成型物件,即把冶炼好的液态金属,用浇注、 压射、吸入或其它浇铸方法注入预先准备好的铸型中,冷却后经打磨等后续加工手段后, 所得到的具有一定形状,尺寸和性能的物件,包括床身、工作台、立柱等。钣焊(金)件 是一种针对金属薄板的综合冷加工工艺,包括剪、冲/切/复合、折、焊接、铆接、拼接、 成型等,包括内外防护、刀库支架等。精密件是实现机械传动的具体实施者,它的优劣直 接影响机械传动的精度、效率等功能,包括主轴、轴承、滚珠丝杠等。功能部件指的是在 机械装配过程中,这些零件先被装配成部件,然后才进入总装配,包括机械手、回转工作台等。电器元件是各种机床控制电路及自动控制系统的基本组成元件,数控系统指通过利 用数字、文字和符号组成的数字指令来实现一台或多台机械设备动作控制,它所控制的通 常是位置、角度、速度等机械量和开关量,也是数控机床中价值量最高的部分。
数控机床:通用制造业核心设备,逐步由“大”到“强”
国内机床产业目前仍然“大而不强,高端失守”。(1)机床产业规模超 7000 亿元:据 国家统计局,2020 年我国机床工具规模以上企业总营收超 7000 亿元,其中金属切削机床 营收超 1000 亿元,整体规模可观。(2)机床数控化率低:据纽威数控招股说明书,2020 年,日本机床数控化率超过 90%,德国机床数控化率超过 75%,美国机床数控化率超过 80%,根据国家统计局数据,我国 2020 年新生产金属切削机床的数控化率仅为 43%。(3) 高端机床国产化率低:根据前瞻产业研究院,2018 年我国低档数控机床国产化率约 82%, 中档数控机床国产化率约 65%,高档数控机床国产化率仅约 6%。但是随着我国工业结构 的优化升级,数控机床市场将由普通机床向数控机床、由低档数控机床向中高档数控机床 升级。在此升级过程中,国产高端机床的市场潜力巨大。
数控机床与通用周期高度一致,头部厂商集中化提升,国产厂商加速替代。数控机床 与通用周期高度一致,根据 MIR(睿工业)及我们系列报告观点,预计 2023-2024 年将迎 来复苏周期。头部厂商销售增长快于机床整体,头部化趋势显现,国产机床逐渐占据一席 之地。根据 MIR,2021 年出货量前 15 名的品牌中,内资品牌占据 10 名,而外资仅占 5 名。内资前三依次为台群精机(创世纪)、海天精工、北京精雕。
国产数控机床销售量占比显著高于销售额,表明价格整体低于外资,科德为高端机床 产品领导者。根据 MIR 统计,按照销售量来看,2021 年国内市场销量前 7 均为国产机床, 分别有台群精机(创世纪)、北京精雕、海天精工、纽威数控、润星科技(华东重机)、宝 鸡机床(秦川机床)和沈阳机床。销售量占比显著高于销售额表明价格整体低于外资,国 产机床仍需要加速高端化,科德数控是国产高端机床的领导者,机床单价远高于国内平均 水平,2020 年单价达到百万元以上。
数控系统:工业母机之魂,自主可控之基
数控系统被称为数控机床的“大脑”,根据国盛智科招股说明书,数控系统约占数控 机床成本的 20%。数控系统通常由控制系统、伺服系统和检测系统三个部分组成,三个系 统通力协作,满足不同机床设备的高要求性能,为机床整体性能提供支撑。我国数控系统 国产化率较低,未来有较大的国产替代空间,目前主要的国产数控系统上市公司有华中数 控和科德数控。
数控系统和数控机床高度绑定,目前我国数控系统可分为经济型、标准型以及高档型 三种类型,经济型增长缓慢,未来增量主要来源于标准型和高档型,华中数控和科德数控 分别是标准型和高档型的代表。数控系统与数控机床高度绑定,也将引领新一轮复苏周期, MIR 预测 2025 年国内市场规模将超过 150 亿元。根据中国机床工具工业协会数据,按销 售套数计算,国外品牌总体占有率约 45%,但占据了高档型、标准型数控系统 70%的份 额。高档型数控系统关键在于技术水平,产品附加值极高,市场主要由德国西门子占据。 标准型数控系统关键在于产品可靠性,产品附加值较高、稳定性高,市场主要由日本发那 科占据。经济型数控系统主要取决于产品价格,进入门槛较低,主要以国产品牌广州数控 为主。
刀具:工业牙齿,通用设备中的耗材
刀具是机床的核心金属零部件,任何切削机床均密不可分,行业存在 know-how,硬 质合金刀具占比有望提升。刀具是机床等切削设备中的必需耗材,根据中国机床工具工业 协会,近年来消费量占金属切削机床消费量的比重不断上升,甚至逼近一半的水平;硬质 合金刀具和其他刀具大约各占一半市场,下游应用各不相同,硬质合金刀具综合性能更好, 预计未来占比将逐步提高;刀具主要壁垒均为金属/非金属原材料的配比、粘合、烧结、成 型及涂层工艺,同时有一定的设备壁垒;全球刀具的绝对龙头是山特维克,其旗下的可乐 满品牌是最为主流和高端的硬质合金刀具品牌;目前内资硬质合金刀具主要厂商中钨高新、 欧科亿、华锐精密等已进入第二梯队,各项产品参数与山特维克差距已经很小,主要差距 在于场景适配性、产品多样性以及后续服务等,有望加速国产替代。
国内刀具市场规模未来均有望快速增长,关注市占率快速提升及产能充足的公司。刀 具是机床的耗材,其消耗量与存量机床呈正比,占增量切削机床的比例呈现逐年提升的态 势。根据中国机床工具工业协会统计的机床数量和 MIR 的预测,可以推算未来的存量机床数,由此我们预测了 2022-2024 年的刀具市场规模,预计 2022/23/24 年的同比增速为 -4.8%/6.2%/6.9%。近年来部分国产刀具厂商实现了份额翻倍,2018-2021 年国内刀具市 场厦门金鹭(厦门钨业)和欧科亿几乎都实现了市占率翻倍,其他主要上市公司还包括中 钨高新和华锐精密,然而目前国产厂商替代率仍然不高,未来替代空间充足,相对来说欧 科亿产能更为充足。
工业机器人产业链:国产替代下提升自动化率的关键 设备
工信部等多部委近日联合发布《“机器人+”应用行动实施方案》,力争到 2025 年, 制造业机器人密度较 2020 年实现翻番,工业机器人是机器人的主体。由于自动化水平的 提升和人力成本的快速上升,根据国家统计局,我国机器人 2015 年开始得到较快产业化, 机器人密度由 2015 年的 51 台/万人提升至 2020 年的 246 台/万人,2023 年 1 月工信部等 多部委近日联合发布《“机器人+”应用行动实施方案》,目标 2025 年国内机器人密度较 2020 年实现翻倍。机器人包括工业机器人、服务机器人、特种机器人和移动机器人等, 各类机器人的应用场景不同,但核心零部件与制造环节接近,目前工业机器人占主要市场 规模,未来服务机器人、特种机器人行业应用深度和广度有望显著提升,移动机器人也将 得到快速发展。
工业机器人成本不含系统集成部分,上游核心零部件成本就已经达到了 70%以上。根 据 Ofweek 网及《中国工业机器人产业发展白皮书》(中国机电一体化技术应用协会,2020), 减速器成本最高,达到 36%,伺服系统占比 24%,控制器占比 12%,三大核心零部件成 本基本呈 3:2:1。从毛利率来看,也是减速器毛利率最高,伺服系统和控制器次之,而 本体的毛利率则最低,为 15%,下游的系统集成毛利率为 35%。
“四大家族”在机器人领域绝对领先,其产业链一体化发展也值得国内企业借鉴。根 据 MIR,工业机器人“四大家族”占据全球一半以上的市场空间,且目前均不同程度上布 局了运动控制和各类机器人全产业链。相对而言,库卡的产业链一体化布局最弱,专注于 机器人及相关技术和零部件;发那科不仅力求全产业链布局,还大力推动全球化策略,全 球建立生产和销售基地,并推动产品高端化转型。所以从财务角度来看,发那科利润率最 高,而库卡最低,其核心原因在于一体化和规模优势越显著,则公司定价能力、全球供应链综合排产能力以及应对市场波动风险的能力均会提升。
工业机器人本体:国产市占率提升,即将迎来市场出清
工业机器人本体结构是指机体结构和机械传动系统,也是机器人的支承基础和执行机 构,中国机电一体化技术应用协会数据显示本体市场空间已达到 400 亿元以上。工业机器 人按照结构类型分为多关节机器人、坐标机器人、SCARA 机器人、并联机器人、工厂用 AGV/AMR 等。根据高工机器人统计,国内主要使用多关节机器人、坐标机器人和 SCARA 机器人,其中坐标机器人国产率较高,目前超过 60%;而 SCARA 和多关节国产率较低, 替代空间大, 近年来增量显著;多关节同质化产品多,是内外资争夺的重点;工厂用移动 机器人增速较快,是物流自动化的关键产品。机器人本体的硬件技术已经趋于成熟,主要 在结构的优化和使用体验的提升,目前国内仍处于增长期,夺取增量是国产替代的重要手 段。
国内工业机器人销量与通用板块周期关联度较高,目前站在新一轮周期的起点,预计 2023 年整体前低后高。国内工业机器人在 2015 年后加速产业化,但呈现出周期性增长, 周期走势与通用板块基本一致。当前在海外需求收缩的背景下,工业机器人站在了新一轮 复苏周期的起点,工业机器人现仍处于“成长性”阶段的自动化产品,预计未来几年仍将 保持 2 位数增长,MIR 预计 2023 年市场仍将承压,此后有望迎来强势反弹。
从国内工业机器人出货的市场格局来看,机器人本体仍然以国外厂商为主,但国产厂 商份额已呈现逐步提升的趋势。尽管美的集团全资收购了库卡,但库卡的主要生产基地都 在国外,如果将库卡算作外资的话,结合 MIR 数据,2022 年国内市场外资占有率达 65% 以上,国产替代仍有较大空间。国内厂商中,埃斯顿和汇川技术市占率已接近“四大家族”, 且具有较好的盈利能力,目前具有较强出货能力的国产上市公司还包括埃夫特、新时达、 爱仕达(钱江)、华中数控(华数)、机器人(新松)和大族激光(大族)。
移动机器人严格意义上不属于工业机器人,但由于其使用场景主要是工厂的物流环节, 所以具有较强的通用属性,类似于叉车,且目前对于人力成本的节省效果显著,增速迅猛, AGV(自动导引运输车)/AMR(自主移动机器人)是移动机器人的两种主要形态。根据 MIR 预测,由于移动机器人在工厂物流环节的性价比优势,移动机器人将迎来快速增长,GGII 预测至 2026 年,移动机器人市场规模 CAGR 将达到 40%以上。AGV(自动导引运 输车)和 AMR(自主移动机器人)是移动机器人的两种主要形态,AMR 主要在 AGV 的 基础上增加了机器视觉。目前国内移动机器人市场主要被外资厂商占据,包括欧姆龙旗下 的爱德普,以及被美的收购的库卡,还有德马泰克、MiR 等。除了美的旗下的库卡,主要 国产上市公司包括海康威视、科大智能(华晓精密)、机器人(新松)、赛象科技(井源机 电)、昆船智能、兰剑智能和工业富联(富士康)等。
控制器:机器人的大脑,自主可控的关键
控制器是工业机器人控制系统的核心大脑,更是决定机器人功能和性能的主要因素, 其主要任务是控制工业机器人在工作空间中的运动位置、姿态和轨迹、操作顺序及动作的 时间等。控制器主要包括硬件和软件两部分:硬件部分是工业控制板卡,包括主控单元和 部分信号处理电路;软件部分主要是控制算法、二次扩展开发等。一般来讲,每台多轴机 器人由一套控制系统控制,也意味着控制器性能要求越高。
由于控制器相对其他核心零部件成本占比较小,所以工业机器人领域控制器市场规模 相对较小,根据 MIR 数据,目前在 30 亿元左右。从市场份额来看,据此前工控领域的统 计,国外品牌还是占据大多数,现在国产品牌的市占率可能有所提升。控制器国产替代较低,是因为机器人控制器和本体绑定效应强,单纯做控制器难以突围,成熟机器人厂商一 般自行开发,以保证稳定性和维护技术体系。
从事控制器的国内厂商较多,而市占率较低的主要原因是控制器往往与本体绑定,本 体厂商一般均有控制器产品,如四大家族及其他机器人本体厂商等。控制器整体技术难度 较小,是国内厂商与国外巨头技术差距最小的零部件,但这部分零部件很难国产替代,因 为控制器真正的国产替代需要本体的国产替代,而这一过程还相当漫长。在机器人厂商中, 埃斯顿收购了英国 TRIO 公司,已实现控制器自主供应;在专业控制器生产商中,雷赛智 能同时开发控制器和伺服驱动,已成为众多本体厂商的供货商。
精密减速器:机器人最关键的传动装置,同时受益于人形机器人发展
精密减速器作为机器人和机床的核心金属零部件,也是成本的主要占比,产品质量对 于提升整机控制精度作用巨大,高端产品均具有非常高的制造门槛。精密减速器是工业机 器人的最大成本项,主要分为谐波减速器和 RV 减速器,由于减速原理的不同,在下游应用中各有所长;但行业壁垒均为加工和装配精度以及材料的性能,非常依赖于长期技术积 累和精密加工设备;日本在减速器领域全球领先,目前谐波中绿的谐波相较于哈默纳科在 高端领域略有差距,RV 中内资厂商相较于纳博特斯克差距较大。
国内精密减速器市场规模未来均有望快速增长。根据 MIR 统计及预计,国内精密减速 器市场规模有望从 2021 年的 101 万台增长至 2024 年的 168 万台,其中 RV 减速器从 55 万台增加至 89 万台,谐波减速器从 47 万台增加至 79 万台,谐波减速器增速更加明显, 主因人型、协作等机器人对谐波减速器更高的使用量。
近年来精密减速器整体国产替代速度较快,RV 减速器有望加速替代。RV 减速器目前 国产替代率不高,外资厂商仍占据一半以上市场,根据 MIR 预测,在双环传动、秦川机床 和南通振康等厂商的冲击下,未来 2-3 年将加速国产替代,但 RV 减速器领域的国产替代 仍以中低端为主。谐波减速器的替代加速较早,近年来进入了高速替代期,这也导致了市 占率统计数据时效性较差导致误差;我们根据哈默纳科中国公司公布的营业收入,并假设 其减速器均价 2500 元/个,且 MIR 预测哈默纳科 2024 年相比于 2021 年国内出货同比增 速为 15%,由此计算得到哈默纳科 2018/21/24 年国内出货分别为 9.9/11.2/12.9 万台,市 占率分别为 33%/21%/14%;哈默纳科 2018-2021 年的市场份额主要被来福谐波挤占, 2021-2024 年将加速国产替代,其中绿的谐波目前已经市占第一。
激光设备产业链:高成长性,国产设备具有相对优势
激光产业链分为上中下游,下游切割、焊接在各行业的设备应用贡献了主要市场规模, 而中游的激光器,决定了激光设备的技术水平。激光设备产业链较为复杂,下游激光设备 主要应用于切割、焊接等环节,应用行业众多,通用设备属性较强。中游环节中,激光器 是激光设备的核心,目前激光器以光纤激光器和半导体激光器为主。光纤激光器和半导体 激光器所对应的上游原材料主要有光学元件和器件以及相关材料,最为核心的是激光芯片 及其叠阵产品。此外,激光控制系统也十分关键,是通用激光设备运动控制的核心。
激光器:激光设备的核心,竞争较为激烈,集中度逐渐提升
激光技术起源于 20 世纪 60 年代,激光器是激光的发生装置,主要由泵浦源和具有 亚稳态能级的增益介质组成。泵浦源为实现并维持粒子数反转产生跃迁辐射创造条件,泵 浦方式主要有电泵浦、化学泵浦、光泵浦、气动泵浦四种,其中光泵浦和电泵浦应用最为 广泛。泵源产生的能量传输至增益介质中,增益介质可以是固体(如 YAG、半导体、光纤)、 气体(如 CO2)或液体(化学溶液)。增益介质中的粒子被激发到较高的激发能级,实现 离子数反转,反转后的粒子以辐射形成从高能级转移到基态后从纤芯中输出激光。激光器 中常见的组成部分还有谐振腔,谐振腔为关键的组成部分,可使腔内的光子有一致的频率、 相位和运行方向,还能改变谐振腔长度来调节所产生激光的模式。除了按照增益介质分类, 激光器也可以按照工作性质分位连续和脉冲,按照输出功率分为高、中、低,按照输出波 长分为红外、可见光、紫外等。
目前激光器以半导体激光器和光纤激光器为主。根据 Laser Focus World的统计,2020 年全球半导体激光器和光纤激光器的市场占比达到了 68%,半导体激光器和光纤激光器具 有结构简单、转换效率高、输出功率高等特点。半导体激光器既可直接作为激光器使用, 也可作为光纤激光器和固体激光器等需要使用光进行激发的激光器的泵浦源。半导体激光 器的核心零部件是激光芯片以及光纤耦合模块,激光芯片通过电泵浦的方式产生能量光束, 通过光纤耦合集中输出。将多个半导体泵浦源尾纤可以集成到单个激光器上,从而提升激 光器的精度和亮度。
全球激光器市场稳步增长,中国激光器市场及国产化率持续提升,中国激光器与通用 板块周期高相关,预计将引来新一轮增长。根据中国科学院武汉文献情报中心统计,目前 全球激光器市场规模已超过千亿元人民币,中国激光器市场规模占比不断提升,已超 70%。 同样根据中国科学院武汉文献情报中心统计,2021 年我国 1.5KW 以下光纤激光器国产化 率已超过 80%,1.5KW 以上光纤激光器国产化率已超 85%,并且还将持续提升。国内激 光器市场规模不断提升,但增速与通用制造业增速高度相关,我们预测激光器将随通用制 造业一同复苏。
国产光纤激光器市占率快速提升,激光器相关上市公司也快速增加。据中国科学院武 汉文献情报中心《2021 中国激光产业发展报告》统计,中国本土激光快速发展,加快国 产替代,尽管 2021 年 IPG 集团 仍位居第一,但市场占比下滑至 42%;位居第二、第六 位的中国本土上市公司锐科激光、杰普特积极抢占市场份额,未上市的创鑫激光也有较高 市占率。此外,其他激光器相关上市公司也快速增加,其中长光华芯是核心国产激光芯片 供应商,激光器其他元器件还包括光纤、光栅、光学晶体等。
激光控制系统:包含伺服系统和振镜系统,玩家少而精
激光控制系统作为激光加工设备的“大脑”,决定了设备的精度、效率,本质上就是 应用于激光的工控系统,主要分为伺服系统和振镜系统。激光加工设备必须要进行运动控 制,激光加工设备的控制系统本质上就是应用于激光的工控系统,但其需要适配于激光加 工的精度及环境要求。振镜由 X-Y 光学扫描头、电子驱动放大器和光学反射镜片组成,电 脑控制器提供的信号通过驱动放大电路驱动光学扫描头,从而在 X-Y 平面控制激光束的偏 转,振镜控制系统主要应用于激光标刻、激光精密切割、激光焊接及其他微加工领域,区 别于在普通激光加工中的伺服系统。
中低功率激光切割控制系统已实现国产替代,国外厂商仍在高功率领域占据绝对优势, 代表厂商为柏楚电子和金橙子。根据柏楚电子公告,国产激光切割控制系统具有较高性价 比,在稳定性、可靠性、精度、速度、易用性等方面已具备优势,因此国内龙头(柏楚电 子、维宏股份、奥森迪科)的中低端激光控制系统已在国内完成国产替代,市占率约为 90%, 其中柏楚电子约占 60%。然而,由于国内行业整体起步较晚且国外厂商在数控系统、高端 制造等领域技术领先,国内高功率激光控制系统市场仍被德国倍福、德国 PA、西门子等国外公司垄断,市占率超 80%。根据金橙子公告,在振镜系统领域,金橙子总体市占率 30%以上,基本完成了中低端的国产替代,但在中高端领域,仍被德国公司垄断,将发力 中高端的国产替代。
激光设备:主要应用于切割,下游需求较为强劲
激光设备高速增长,增速变化幅度与通用制造业一致。相对于传统加工工艺,激光加 工具有适用对象广、材料变形小、加工精度高、低能耗、污染小、非接触式加工、自动化 加工等优点,目前已成为一种新型制造技术和手段。欧美主要发达国家在机械、汽车、航 空、钢铁、造船、电子等大型制造产业中,已开始大规模使用各项激光加工工艺。受益于 我国制造业升级,国内激光加工市场保持稳定增长,根据激光行业观察微信公众号《2022 年中国激光设备行业研究报告》,目前市场总体规模已接近千亿,报告预计 2026 年市场规 模将接近 2000 亿元。
激光设备市场一超多强,各公司主要应用领域侧重有所不同。受益于新能源产业的快 速发展,我国激光设备市场国产化率不断提升,目前国内厂商呈现一超多强的态势。根据 激光行业观察微信公众号《2022 年中国激光设备行业研究报告》,2021 年大族激光是行业 龙头,华工科技、海目星、联赢激光、帝尔激光和光韵达的市占率均在 1%以上。各公司 侧重行业略有不同,大族激光已成为立足于多行业的平台型激光公司,华工科技主要从事 汽车领域,联赢激光专注于激光焊接,海目星主要从事锂电设备,帝尔激光从事光伏设备。
成形设备:包括注塑、压铸、压力、锻压设备等
注塑机:主要服务于橡塑工业,增速较为稳定
注塑成型技术是塑料产品制造的主要方式,近年来我国注塑成型装备市场规模稳步增 长。注塑机是指将热塑性塑料或热固性塑料利用塑料成型模具制成各种形状的塑料制品的 主要成型设备。注塑机由注射系统、合模系统、液压传动系统、电气控制系统、润滑系统、 加热及冷却系统、安全监测系统等组成。根据中国塑料机械工业协会统计,2021 年我国 注塑成型装备市场规模已经达到了 243.8 亿元,相较于 2016 年 211.6 亿元的行业规模,5 年 CAGR 为 2.87%,基本与塑料行业增速一致。根据中国塑料机械工业协会的预测,预 计未来几年我国注塑成型装备市场规模将以不低于 2%的年增速稳步增长,2024 年市场规 模有望突破 260 亿元。
国产注塑机技术进步,逐渐替代进口,切入汽车行业为主的高端注塑机市场。过去我 国注塑机企业主要占据中低端市场,在高端市场领域,注塑成型装备主要应用于汽车行业, 过去汽车行业注塑机主要以恩格尔、克劳斯玛菲(已被中国化工科学研究院收购)、住友 等海外品牌为主。在当前汽车产业轻量化、电动化的大趋势下,采用塑料能够减轻汽车自 重,从而达到降低汽车排放、提高燃油效率的效果。近年来国产新能源车企快速崛起,整 车销量占比显著提升,带动国内汽车零部件企业崛起,逐渐取代外资高端整车和零部件企 业份额。同时国内注塑机产品不断进步,在高端市场正在逐步缩小与外企的差距。随着国 产整车和零部件企业崛起以及国产注塑机技术不断进步,海天、伊之密、力劲等国产注塑 机企业不断切入汽车行业为主的高端注塑机市场,开始逐步替代外资高端品牌。
海天是国内注塑机行业龙头,伊之密跃居行业第二。根据中国塑料机械工业协会的数 据,2021 年我国注塑成型装备市场规模达到 243.8 亿元,同期海天国际注塑机板块的国 内市场营收达到了 110.9 亿元,2021 年海天国际在国内注塑机行业市场份额达到了 45.5%, 为国内行业龙头。伊之密近年来通过持续加大技术投入,在注塑机行业的市场份额持续提 升,2021 年已超越震雄集团,注塑机业务收入规模跃居国内第二。
压铸机:受益于一体化压铸趋势,未来市场空间广阔
2020 年我国传统压铸机市场规模在 30 亿元左右,受益于铝替代钢而总体呈持续增长 趋势。我国制造业规模全球第一,也是世界上最大的压铸机市场。全国压铸机市场规模没 有明确的统计数据,我们根据中铸科技公布的 2019 年国内压铸机市场份额以及行业龙头 力劲科技压铸机业务历年收入和内销占比大致推算行业空间。我国压铸机市场总体呈增长 趋势,市场规模从 2012 年的 17 亿元增长至 2020 年的 30.5 亿元,CAGR 为 6.7%,说明 受益汽车行业规模扩大以及铝代钢带来压铸件占比提升,压铸机需求在缓慢扩大中。根据 中铸科技官网,力劲科技占据国内压铸机的半壁江山,目前伊之密的市占率也在不断提升。
预计到 2030 年全球压铸机及相关设备市场规模将从 2020 年的 75 亿元增长至 713 亿元,压铸机已主要应用于汽摩领域,通用属性减弱,一体压铸将使全球压铸机市场持续 高增长。根据中国压铸网,中国约占全球压铸机市场的 40%左右,因此我们根据我国 2020 年压铸机市场 30.5 亿元的市场规模,假设全球传统压铸机市场规模 2020 年为 75 亿元。 力劲科技公告显示其 2020-2023 年营业收入 CAGR 为 27%,由于一体压铸需求的拉动 我们假设未来十年行业需求复合增速为 25%,我们预计到 2030 年全球压铸机及相关设 备市场规模约 713 亿元;其中预计一体压铸的占比将持续升高,一体压铸需求将使全球 压铸机市场在未来十年持续高增长。一体压铸主要应用于汽车生产领域,压铸机行业的通 用属性将减弱,但整体注塑、压铸等成型设备也将受到通用板块复苏的利好。
压力机:包括通用压力机及专业压力机,部分下游行业需求高景气
压力机是最主要的金属成形设备之一,也分为通用压力机和专用压力机,包括冲床、 液压机、冷镦机等。压力机(包括冲床、液压机)是一种结构精巧的通用性压力机。具有 用途广泛,生产效率高等特点,压力机可广泛应用于切断、冲孔、落料、弯曲、铆合和成 形等工艺。通过对金属坯件施加强大的压力使金属发生塑性变形和断裂来加工成零件。机 械压力机工作时由电动机通过三角皮带驱动大皮带轮,经过齿轮副和离合器带动曲柄滑块 机构,使滑块和凸模直线下行。机械压力机在锻压工作完成后滑块程上行,离合器自动脱 开,同时曲柄轴上的自动器接通,使滑块停止在上止点附近。
从国内市场来看以压力机为主的金属成形设备市场规模较为稳定,预测未来呈现稳步 上升态势等。压力机是最主要的金属成形设备,而注塑机则往往从事非金属的成形工作。 根据 MIR 数据,目前以压力机为主的国内金属成形设备市场规模已达到 600 亿元以上, MIR 预测未来市场规模呈现稳步上升态势。
压力机伺服化是目前压力机的一大趋势,伺服压力机为新一代智能成形装备,性能超 越传统压力机。伺服压力机由伺服电机进行驱动控制,可以任意编程滑块的行程、速度、 压力等。相比传统压力机,伺服压力机冲速更高,且可根据冲压产品设定不同曲线,实现 自动化柔性控制,从而提高加工效率与精度,节约能耗成本,广泛适用于各种复杂冲压件 高效生产和轻量化材料的冷热成形。
全球伺服压力机市场回复稳定增长,国内渗透率仍有提高空间。根据亚威股份公司公 告及 QY Research,2022 年,全球伺服压力机消费额达 89.48 亿元,同比增长 5%,未来 预计同步金属成型企业数字化转型趋势,保持稳定增长;2021 年,日本伺服压力机渗透 率为 95%,欧洲渗透率为 40%-50%,国内渗透率水平仍远低于国际,主要由于大多本土 机床厂商不具备技术优势,同时成本端承压导致产量受限,未来随国产数控技术突破、下 游产品需求复杂化、国家节能政策引导,国内伺服压力机市场有望出现井喷式增长。伺服 冲床主要玩家包括德国舒勒、日本会田、日本天田、日本小松、中国台湾金丰、中国台湾 协易等,以外资厂商为主,国产替代空间大。
国内压力机的主要厂商的技术路线和从事领域略有不同,多数销售规模较小,有待提 高集中度和国产化率。国内压力机厂商包括上市公司中的亚威股份、宁波精达、思进智能、 合锻智能等,非上市公司包括扬州锻压、天津锻压、济南二机床等,各厂商的技术路线和 从事领域略有不同,如亚威股份主要从事通用压力机、折弯机及冲床,宁波精达主要从事 专用压力机、思进智能主要从事冷镦成形设备、合锻智能主要从事液压机等,各厂商各有 所长,但整体规模较小,有待进一步提升集中度及国产化率。
叉车:国产叉车出海及电动化趋势显著
预计国内需求底部复苏在即。叉车需求主要来自制造业、物流业需求。根据中国工程 机械协会,我国叉车销量从 2011 年的 31.4 万辆增长至 2021 年的 109.9 万辆,CAGR13.3%。 受益于国内制造业+物流业规模扩大、渗透率提升、全球竞争力提升三大逻辑,我们预计 我国叉车市场规模未来 5~10 年仍将保持 10%左右的年均复合增速。同时短期内叉车需求 与 PMI 等经济景气指标一致,从历史上看存在 3 年左右的行业需求周期。本轮叉车景气周 期下行始于 2021 年三季度,2022 年二季度的局部疫情反复加重了行业需求的低迷,但随 着国内疫情政策进一步优化和生产的恢复,叉车需求从 2022 年四季度开始逐步复苏进入 上行阶段。
锂电平衡重叉车引领新增长点,龙头公司安徽合力和杭叉集团收入增速高于销量增速。 平衡重叉车锂电化以及油价上涨带来经济性提升,国内平衡重叉车快速电动化;根据中国 工程机械协会,我国电动平衡重叉车在平衡重叉车中的渗透率从 2020 年的 16.4%提升至 2022 年前五个月的 21.9%,较欧洲的 58%仍有较大提升空间。电动平衡重叉车单价基本 为燃油平衡重叉车的 2 倍,平衡重叉车快速电动化,龙头公司安徽合力和杭叉集团收入增 速料将快于销售台数增速。我们预计 2023 年龙头公司叉车销量同比增长 10%左右,考虑 到高价值量的电动平衡重叉车国内渗透率提升,我们预计 2023 年龙头公司国内收入同比 增长 15%左右。
锂电化带动中国叉车全球竞争力提升。随着锂电池技术的不断成熟,锂电池逐渐取代 铅酸电池成为电动叉车主流技术路线,根据安徽合力的投资者调研纪要,2021 年我国锂 电池叉车在电动平衡重叉车和电动仓储式步行叉车的占比分别达到 42.8%和 53.2%。过去 中国叉车出口主要以价值量较小的电动步行式仓储叉车为主(2020 年出口台数占比 60%); 高价值量的平衡重叉车领域,受限于内燃叉车发动机和变速箱的技术,我国企业与海外巨 头丰田、凯傲相比存在技术劣势。但 2021 年以来,随着平衡重叉车锂电化以及油价上涨 带来的经济性提升,利用国内成熟的新能源车产业链技术,我国叉车企业在锂电平衡重叉车领域竞争优势显著,弯道超车海外巨头。
钢价下降对盈利能力有显著拉升作用。龙头公司安徽合力和杭叉集团毛利率相对较低, 从历史上看,钢材价格上涨将严重影响公司毛利率水平。根据我们对安徽合力的调研,2021 年钢材在公司主营成本的占比达到了 40%;我们做了一个钢价对公司毛/净利率的敏感性 分析测算,得出的结论是在其他条件都不变的情况下,2021 年钢价每下降 5 个百分点, 对应公司的毛利率将提升 4.2 个百分点。钢价大幅下跌有望显著提升公司盈利能力。
增材制造:变革性生产技术,千亿级朝阳产业
增材制造具有较强的通用属性,增材制造理念历史悠久,产业化历程相对短暂。增材 制造,通常俗称为 3D 打印,定义为以数字模型文件为基础,通过软件与数控系统将专用 的金属材料、非金属材料以及医用生物材料,利用软件进行设计和优化,通过专用的打印 设备按照挤压、烧结、熔融、光固化、喷射等方式逐层堆积,制造出实体物品的制造技术。 增材制造核心设备为 3D 打印机,目前增材制造在工业中常被用于航空航天、医疗、模具、汽车等领域特殊零部件制造。增材制造并不是一个全新概念,早在 19 世纪末期美国和法 国就有了关于使用层合方法生成地图模型的方法,但都停留在图纸层面。1986 年 3D Systems 成立,标志着增材制造进入产业化。1995 年德国 Fraunhofer 激光技术研究所(ILT) 推出 SLM 技术,激光技术开始被应用于增材制造并逐步普及。整体来看我国增材制造产 业化相对短暂,但随着美欧的 3D 打印底层技术专利在 2009-2015 年陆续到期,我国增材 制造市场开始进入发展快车道。根据中国增材制造产业联盟,2022 年我国 3D 打印市场规 模有望达到 330 亿元。
增材制造使用材料逐步累加形成需要产品,和传统制造拥有本质区别。增材制造与传 统制造的最大差别在于传统制造使用车、铣、刨、磨、钻等工具依靠机械外力实现多余材 料去除,或者直接使用铸造和锻造工艺实现产品制造与加工,而增材制造则是使材料一点 点累加形成需要的形状。原理上的本质差异使得增材制造和传统制造在原料使用、技术设 备、应用领域方面均有一定差异。
我国增材制造 2021 年规模达 262 亿元,仍处于快速发展通道。随着美欧的 3D 打印 底层技术专利在 2009-2015 年陆续到期,我国增材制造行业专利授权量快速增长,推升行 业景气度。叠加政策、要素成本以及下游需求的拉动,我国增材行业近年来实现快速增长。 根据中国增材制造产业联盟,2021 年我国增材制造产业规模达 262 亿元,2018-2021 年 CAGR 为 29%。根据赛迪咨询,2024 年中国 3D 打印市场规模有望突破 500 亿元,相较 2021 年同比提升 91%,2021-2024 年 CAGR 为 24%。
产业链以中游设备商为核心,厂商丰富,上市公司较少。市场化需求衍生出完整产业 链,增材制造以技术为关键,设备为核心,产品为最终体现形式,整体产业链可以分为上 中下游。从上市公司角度来看,上游领域主要是生产所需原材料和增材制造设备的核心硬 件和辅助设备,原材料主要为金属粉末和非金属材料,主要上市公司有铂力特、有研新材; 硬件为核心的激光器、振镜系统和引擎,主要上市公司有大族激光、锐科激光、金橙子; 辅助设备主要包括 3D 建模软件和扫描仪,主要厂商有铂力特。中游即为增材制造设备, 增材制造的核心是中游的设备制造,设备按照原材料类别可分为金属打印和非金属打印,金属领域的主要上市公司有铂力特,非金属领域的主要厂商有拟上市的华曙高科。下游主 要为各应用领域,航空航天、医疗、汽车、高校科研院所为主要应用领域,主要上市公司 有航空航天的超卓航科,以及涵盖多个上市主体的中航工业,汽车领域的一汽集团,医疗 领域的时代天使。
(本文仅供参考,不代表我们的任何投资建议。如需使用相关信息,请参阅报告原文。)
精选报告来源:【未来智库】。
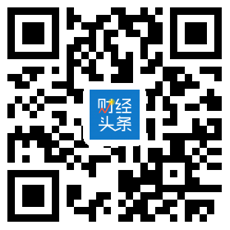
4000520066 欢迎批评指正
All Rights Reserved 新浪公司 版权所有